I have spent the last couple of weeks trying to finish up various works in progress. There's the stocking I made for my kiddo two years ago, but I didn't like the toe so I only sewed it up partially and didn't put on the i-cord trim. Then there's the gansey watch cap I started for my husband in July. And, of course, the infamous Jaywalkers.
I got a lot done. Finished the gansey hat before midnight on Christmas Day. Reknitted the stocking toe and re-seamed it, but did a bad job tacking on the i-cord so I still need to do that. Got some stashbusting in, too--I made myself a neckwarmer out of bulky 3-ply Targhee that has been languishing for a few years in my cedar chest, and made a pair of newborn/small longies for the Venus Vanguard stocking tomorrow. And miracle of miracles, the Jaywalkers have 2"-3" left to go, so I have hopes of getting them finished off tonight.
In business news, I had a successful inventory clearance sale last week, and my first group order of 2009 just opened yesterday at Yarn for Fun, with the second one due to open the first week of February at Designer Dupas Yarn. Halfway through my next wholesale order for Apple Yarns. The year's ending on a good note!
Wednesday, December 31, 2008
Sunday, December 21, 2008
Jaywalker, part 2
I am never, ever going to finish this pair of Jaywalkers that I started in September 2007. Yes, it's been 15 months. Good thing I have plenty of Smartwool socks to keep my feet warm.
After a reasonably good start, I put the project on hold for a few months. Came back to it when I had some downtime from business knitting and finished up the first sock in April or so. Got busy again and didn't pick up the second sock till I went on vacation in October. I couldn't find my instructions for knitting it toe-up, so I thought blithely that I would just knit the second one cuff down. I knew my chevrons would be pointing in the wrong direction, but I thought I'd just rotate it 1/8 or 1/4 or whatever, and then everything would match the other sock.
Stupid, stupid, stupid. Got to the heel, turned it, and realized that my increases and decreases wouldn't cancel each other out. I'd end up with too many stitches, or not enough, or something. No problem--I'd just knit the bottom half of the sock toe-up, and then graft the halves together.
Alas, another solution that I didn't think through! I got to the grafting part. I was a mere 76 kitchener stitches away from a completed pair of Jaywalkers. But then I realized instead of forming nice tidy rows of triangles all pointing in the same direction, grafting would give me little diamonds with bulges of extra sock in their centers.
That's what you get for not doing a project straight through--you forget how the pattern works, make foolish assumptions, and end up with no socks. I'm putting this away for a while till the frustration fades a bit.
After a reasonably good start, I put the project on hold for a few months. Came back to it when I had some downtime from business knitting and finished up the first sock in April or so. Got busy again and didn't pick up the second sock till I went on vacation in October. I couldn't find my instructions for knitting it toe-up, so I thought blithely that I would just knit the second one cuff down. I knew my chevrons would be pointing in the wrong direction, but I thought I'd just rotate it 1/8 or 1/4 or whatever, and then everything would match the other sock.
Stupid, stupid, stupid. Got to the heel, turned it, and realized that my increases and decreases wouldn't cancel each other out. I'd end up with too many stitches, or not enough, or something. No problem--I'd just knit the bottom half of the sock toe-up, and then graft the halves together.
Alas, another solution that I didn't think through! I got to the grafting part. I was a mere 76 kitchener stitches away from a completed pair of Jaywalkers. But then I realized instead of forming nice tidy rows of triangles all pointing in the same direction, grafting would give me little diamonds with bulges of extra sock in their centers.
That's what you get for not doing a project straight through--you forget how the pattern works, make foolish assumptions, and end up with no socks. I'm putting this away for a while till the frustration fades a bit.
Tuesday, December 16, 2008
the last custom of 2008
I mailed a package to a Canadian customer today. Had to go to the post office since it was an international item. I stood in line for 40 minutes. Ugh. I've decided not to do any more international shipments until the holiday insanity is over. This isn't a complaint about the post office, though. I really appreciate the postal staff in town, though--they are always pleasant and helpful, and my regular mail carrier has delivered and taken away an enormous number of parcels in the last two years. Lots of people have horror stories about their shoddy local service, and I am so grateful to live in a place where I never have cause for complaint.
Anyway, here's what was inside the package. I squeezed this one in when another custom order got delayed, and at the same time someone purchased some yarn for me and asked if I had time to knit it up.
This is my new Coldfire colorway, kettle-dyed on Marr Haven wool. It was much more muted than on my Shooting Star sock yarn, probably because the dye struck so much faster on the superwash wool. The colors didn't have a chance to meld together. Also, I think the Marr Haven absorbs a lot of dye.

This is my second project with Marr Haven. I was struck again by the similarities to Sweet Grass Wool's worsted Targhee. They are both mule spun, so I wonder how much the processing accounts for it. Both have a soft, furry texture but not much elasticity.
Anyway, here's what was inside the package. I squeezed this one in when another custom order got delayed, and at the same time someone purchased some yarn for me and asked if I had time to knit it up.
This is my new Coldfire colorway, kettle-dyed on Marr Haven wool. It was much more muted than on my Shooting Star sock yarn, probably because the dye struck so much faster on the superwash wool. The colors didn't have a chance to meld together. Also, I think the Marr Haven absorbs a lot of dye.

This is my second project with Marr Haven. I was struck again by the similarities to Sweet Grass Wool's worsted Targhee. They are both mule spun, so I wonder how much the processing accounts for it. Both have a soft, furry texture but not much elasticity.
Monday, December 15, 2008
protecting the stash against moth invaders
I know in my head that only certain types of moths will harm my yarn and wool clothing. But around here, no moth is shown any form of mercy--just in case.
Given my paranoia about moths, I was very interested in a recent article by Oregon State University Extension on alternatives to mothballs. If you're not familiar with Extension, each state was granted land by the federal government to fund a designated university to conduct research-based outreach to that state's citizens. Extension was originally focused on agricultural issues--pest management being a significant element, of course--but has since expanded to include home gardening (the Master Gardener program is a prime example), water quality, 4-H, nutrition, and parenting, among other issues. There is also a new program to train citizens in climate change issues--but I digress. (I used to work for Extension on water issues, and I think it's a fantastic program.)
Anyway, one of the two major problem moths in this country is a specimen by the name of Tineola bisselliella. When they are at rest, they don't spread their wings like the winter moth, which is the species active in these parts at this time of year, but fold them up into a rectangular shape.
One of the article's recommendations is to sun your clothing once or twice a month. It doesn't mention the most common recommendation that I've heard for safeguarding yarn, which is to freeze it, let it warm up, and then freeze again to kill any larvae that might have emerged during the thaw. We recently bought a chest freezer to store some local grass-fed beef that we just purchased in bulk, as well as the gallons and gallons of berries that we picked this summer, but to tell the truth, I have been toying with the idea of using it for mothproofing my stash. It's big and it's airtight, and it sits oh so temptingly next to my dyeing table. My husband asked if I could move all my undyed yarn in the garage, now that I have dedicated work space there, and I said only if I could put it in the freezer.
Given my paranoia about moths, I was very interested in a recent article by Oregon State University Extension on alternatives to mothballs. If you're not familiar with Extension, each state was granted land by the federal government to fund a designated university to conduct research-based outreach to that state's citizens. Extension was originally focused on agricultural issues--pest management being a significant element, of course--but has since expanded to include home gardening (the Master Gardener program is a prime example), water quality, 4-H, nutrition, and parenting, among other issues. There is also a new program to train citizens in climate change issues--but I digress. (I used to work for Extension on water issues, and I think it's a fantastic program.)
Anyway, one of the two major problem moths in this country is a specimen by the name of Tineola bisselliella. When they are at rest, they don't spread their wings like the winter moth, which is the species active in these parts at this time of year, but fold them up into a rectangular shape.
One of the article's recommendations is to sun your clothing once or twice a month. It doesn't mention the most common recommendation that I've heard for safeguarding yarn, which is to freeze it, let it warm up, and then freeze again to kill any larvae that might have emerged during the thaw. We recently bought a chest freezer to store some local grass-fed beef that we just purchased in bulk, as well as the gallons and gallons of berries that we picked this summer, but to tell the truth, I have been toying with the idea of using it for mothproofing my stash. It's big and it's airtight, and it sits oh so temptingly next to my dyeing table. My husband asked if I could move all my undyed yarn in the garage, now that I have dedicated work space there, and I said only if I could put it in the freezer.
Friday, December 12, 2008
protect small artisans
I've been hearing a lot lately about the Consumer Product Safety Information Act of 2008, a federal law that is intended to protect children under 12 from using products with lead, phthalates, and other hazardous substances. This law applies not just to mass toy manufacturers who import tainted products from China (the original impetus of the law), but also to small-scale artisans making toys and children's items (clothes, diapers, bibs, etc.).
Beginning in February 2009, all of these finished items will now be required to be tested for lead. As of August 2009, testing must be conducted by a third-party certified lab.
As a yarn dyer, I don't have too many concerns that this will affect my business practices. But as someone who loves handmade items made out of natural materials, particularly for my child, I have a great deal of concern that the artisans that I love and support will no longer financially be able to stay in business. Testing ranges from $100 to $4,000 for each batch of identical product. Fines are severe--about $150,000 per violation, I believe.
The following is reposted with permission from the HC forums. I will be sending Rep. Rush an item in the next few days. Although I'm not his constituent, I hope that by being part of a flood of packages, my action may make a difference in his thinking on this law. If your representative belongs to the Commerce, Trade, and Consumer Protection subcommittee, your letter/package will have a particularly strong impact. My own Congressman is on the House Small Business Committee, so I'll probably write him as well.
--------
The idea is to send Rep. Rush (chair of the subcommittee on Commerce, Trade, and Consumer Protection) a handmade product that will be banned after Feb 10. Below is the letter my dad and I are including with our item -- feel free to copy it, and change as you see fit. If you're not a maker of handmade children's items but you are affected by the law as a buyer of such items, you can amend the letter below to reflect that, and maybe send an item that you want to spare, or just amend the letter to include a description of the item....maybe include a picture.
Anyway, here is an example of a correspondence:
Dear Representative Rush:
On Feb. 10, 2009, due to new CPSIA regulations, the enclosed item will turn into a "BANNED HAZARDOUS SUBSTANCE." Don't let this happen! I am an artisan who owns a wooden toy business. I make my products in my home studio using untreated natural wood, non-toxic glue, beeswax, and mineral oil. Even though I use safe, natural materials to make my items, each one-of-a-kind item I make will require testing; however, it is financially impossible for me to comply with the new CPSIA lead testing standards. I will be forced to shut down my toy business. Not only will this affect our family's income, it will affect hundreds of children whose parents prefer handmade, natural toys for their children.
PLEASE consider amending the legislation to exempt from third party testing requirements:
* natural materials such as wood, wool, bamboo, cotton and uncoated textiles.
** toys and apparel handmade in the US, Canada, and the EU that use trusted safety-regulated supplies.
Also, please consider allowing manufacturers to use lead testing certification from suppliers. This would cut down on retesting and make complying financially feasible for micro-manufacturers like myself.
Thank you for your time.
Sincerely,
[your name]
Address:
The Honorable Bobby L. Rush
United States House of Representatives
2416 Rayburn House Office Building
Washington, D.C. 20515-1301
Beginning in February 2009, all of these finished items will now be required to be tested for lead. As of August 2009, testing must be conducted by a third-party certified lab.
As a yarn dyer, I don't have too many concerns that this will affect my business practices. But as someone who loves handmade items made out of natural materials, particularly for my child, I have a great deal of concern that the artisans that I love and support will no longer financially be able to stay in business. Testing ranges from $100 to $4,000 for each batch of identical product. Fines are severe--about $150,000 per violation, I believe.
The following is reposted with permission from the HC forums. I will be sending Rep. Rush an item in the next few days. Although I'm not his constituent, I hope that by being part of a flood of packages, my action may make a difference in his thinking on this law. If your representative belongs to the Commerce, Trade, and Consumer Protection subcommittee, your letter/package will have a particularly strong impact. My own Congressman is on the House Small Business Committee, so I'll probably write him as well.
--------
The idea is to send Rep. Rush (chair of the subcommittee on Commerce, Trade, and Consumer Protection) a handmade product that will be banned after Feb 10. Below is the letter my dad and I are including with our item -- feel free to copy it, and change as you see fit. If you're not a maker of handmade children's items but you are affected by the law as a buyer of such items, you can amend the letter below to reflect that, and maybe send an item that you want to spare, or just amend the letter to include a description of the item....maybe include a picture.
Anyway, here is an example of a correspondence:
Dear Representative Rush:
On Feb. 10, 2009, due to new CPSIA regulations, the enclosed item will turn into a "BANNED HAZARDOUS SUBSTANCE." Don't let this happen! I am an artisan who owns a wooden toy business. I make my products in my home studio using untreated natural wood, non-toxic glue, beeswax, and mineral oil. Even though I use safe, natural materials to make my items, each one-of-a-kind item I make will require testing; however, it is financially impossible for me to comply with the new CPSIA lead testing standards. I will be forced to shut down my toy business. Not only will this affect our family's income, it will affect hundreds of children whose parents prefer handmade, natural toys for their children.
PLEASE consider amending the legislation to exempt from third party testing requirements:
* natural materials such as wood, wool, bamboo, cotton and uncoated textiles.
** toys and apparel handmade in the US, Canada, and the EU that use trusted safety-regulated supplies.
Also, please consider allowing manufacturers to use lead testing certification from suppliers. This would cut down on retesting and make complying financially feasible for micro-manufacturers like myself.
Thank you for your time.
Sincerely,
[your name]
Address:
The Honorable Bobby L. Rush
United States House of Representatives
2416 Rayburn House Office Building
Washington, D.C. 20515-1301
Thursday, December 11, 2008
rainbows
A lovely customer requested some rainbow colorways with no purple in them. So I handpainted a couple, one with brown:


They weren't quite as vivid as I thought she'd like, especially the one with brown. So a few nights later, I redyed the chocolate rainbow (my inaugural skein from my night-ready dye studio):

Much more vibrant. This skein was space-dyed, which I find produces the most even color throughout a skein, and sometimes (as in this case) richer colors. The drawback is that it takes a while for me to do.
The customer likes the more saturated colors, as I thought she would. So I'll be hitting the rainbow dyepots again shortly for another go at the rainbow with no purple. My second Ott-Lite showed up today and makes a big difference, so I'm looking forward to some productive evenings in my new workspace.


They weren't quite as vivid as I thought she'd like, especially the one with brown. So a few nights later, I redyed the chocolate rainbow (my inaugural skein from my night-ready dye studio):

Much more vibrant. This skein was space-dyed, which I find produces the most even color throughout a skein, and sometimes (as in this case) richer colors. The drawback is that it takes a while for me to do.
The customer likes the more saturated colors, as I thought she would. So I'll be hitting the rainbow dyepots again shortly for another go at the rainbow with no purple. My second Ott-Lite showed up today and makes a big difference, so I'm looking forward to some productive evenings in my new workspace.
Wednesday, December 10, 2008
dye studio--trial run
I dyed in my garage dye studio for the first time at night. It went pretty well. For lighting, I had one wide-area Ott Lite (with another one on the way). The second light is definitely going to help, but I was able to angle the first over my work area so that there was adequate light. The light is a little harsh, but the colors do show up quite accurately.
Since my fancy induction burner wasn't going to work out, I had a $30 two-burner hotplate from Target. I used it to steam set some yarn last week, and it worked fine for that. I was space dyeing last night, and it did take a long time to get the water up to the right temperature, but it will do.
It's really nice to have dedicated space, where I don't need to worry about spilling stuff. Michael was the one really pushing to get my studio set up, since he wants to give the kitchen a minor makeover but didn't want to see accidental splotches of dye on all his handiwork. He installed the utility sink, cleaned out the garage, bought me shelving units, and made an executive decision about the burner when I was dithering over what to get. Left to my own lazy devices, I would still be dyeing in the kitchen, but thanks to him, I've got my own space. I'm glad I married him. ;)
Since my fancy induction burner wasn't going to work out, I had a $30 two-burner hotplate from Target. I used it to steam set some yarn last week, and it worked fine for that. I was space dyeing last night, and it did take a long time to get the water up to the right temperature, but it will do.
It's really nice to have dedicated space, where I don't need to worry about spilling stuff. Michael was the one really pushing to get my studio set up, since he wants to give the kitchen a minor makeover but didn't want to see accidental splotches of dye on all his handiwork. He installed the utility sink, cleaned out the garage, bought me shelving units, and made an executive decision about the burner when I was dithering over what to get. Left to my own lazy devices, I would still be dyeing in the kitchen, but thanks to him, I've got my own space. I'm glad I married him. ;)
Wednesday, December 3, 2008
back to the Stone Age
You never really appreciate high-speed internet until you don't have it any more. Since Black Friday, my DSL connection has been ridiculously slow. I couldn't even get a connection on Saturday. I called on Sunday to see if there was some sort of problem; the automated service said there were no network issues, but at that moment my connection was mysteriously restored, and I haven't had any problems with my ISP since. Hmmmm.
But it's still slow. Like, dial-up slow. Maybe even 2400 baud slow, where you can see individual letters typing themselves across the screen. My shopping style has definitely been cramped. And now that I'm trying to upload and, worse yet, edit photos for the Venus Vanguard stocking tomorrow, I am really feeling the pain. I prefer how Picnik handles color corrections to my desktop photo editing programs, but it is taking forever to load photos, and the batch edit option hasn't worked for me for weeks now so Picnik has to relaunch every time for each photo.
Since it was so pokey, I thought I'd give Adobe Photoshop Express another try. Still don't like it. It took even longer than Picnik to launch. And the editing options seem much less flexible and intuitive than Picnik's. For instance, exposure and contrast are bundled together; you can't adjust them separately as far as I can tell. I would definitely not call it Photoshop Lite; it's more like Photoshop Zero.
I did manage to edit my photos of my new soaker ornaments. I think they're pretty darn cute. Though they're not quite shaped like my normal-sized soakers. I am having a hard time resisting the urge to rip them out and redo them. I happened to buy a Christmas wreath today, and it made a nice backdrop for the ornaments.


I also dyed a new colorway this week, Coldfire. It's inspired by C.S. Friedman's trilogy of the same name. Silver, frosty and royal blues, and deep, deep black. I really like it.
But it's still slow. Like, dial-up slow. Maybe even 2400 baud slow, where you can see individual letters typing themselves across the screen. My shopping style has definitely been cramped. And now that I'm trying to upload and, worse yet, edit photos for the Venus Vanguard stocking tomorrow, I am really feeling the pain. I prefer how Picnik handles color corrections to my desktop photo editing programs, but it is taking forever to load photos, and the batch edit option hasn't worked for me for weeks now so Picnik has to relaunch every time for each photo.
Since it was so pokey, I thought I'd give Adobe Photoshop Express another try. Still don't like it. It took even longer than Picnik to launch. And the editing options seem much less flexible and intuitive than Picnik's. For instance, exposure and contrast are bundled together; you can't adjust them separately as far as I can tell. I would definitely not call it Photoshop Lite; it's more like Photoshop Zero.
I did manage to edit my photos of my new soaker ornaments. I think they're pretty darn cute. Though they're not quite shaped like my normal-sized soakers. I am having a hard time resisting the urge to rip them out and redo them. I happened to buy a Christmas wreath today, and it made a nice backdrop for the ornaments.


I also dyed a new colorway this week, Coldfire. It's inspired by C.S. Friedman's trilogy of the same name. Silver, frosty and royal blues, and deep, deep black. I really like it.

Thursday, November 27, 2008
Black Friday surprises
I have a few tricks up my sleeve for tomorrow. I'll be a guest at K&F's birthday celebration, and my congo, Venus Vanguard, is also running a Black Friday sale. Not telling what's going to pop up where--or when--but here are a few sneak peeks:


Hope those of you in the U.S. had a happy and delicious Thanksgiving!


Hope those of you in the U.S. had a happy and delicious Thanksgiving!
Tuesday, November 25, 2008
listen to Buffett--don't underprice yourself
Like a lot of people who make handmade items, I have often struggled with pricing. Sometimes I'm afraid to charge what I'd earn if I made minimum wage, let alone what I think the item is really worth, for fear of scaring off potential customers.
Last year, I read the best pricing advice I've ever heard. I can't find the link, but the basic concept was to never go for the bargain-minded shopper as your principal sales strategy. There will always be someone new who's willing to sell at a lower price than you--and boom, there go your customers. The bargain hunter is not a loyal customer, and isn't the kind of steady long-term clientele that you want for your business.
I found affirmation of this idea from a surprising source--Warren Buffett. Earlier this month, I read a Wall Street Journal story that interviewed Buffett. This paragraph jumped out at me:
"We do try to buy our businesses like we buy our stocks," Mr. Buffett told me, "and buy our stocks like we buy our businesses." By that he means, among other things, that he wants to understand how the enterprise generates cash, how well-managed it is and whether its customers would stay loyal even if it raised the prices of its goods or services.
There you have it. Unless you're able to make it up on sales volume, you'll never make it in any line of business, handmade or not, if you try to compete on a pricing basis--there are too many other sellers who are willing to take less than you. Go for quality, customer service, honing your own unique style, and figuring out other ways to build customer loyalty--and maybe someday Buffett will invest in you. Hey, you never know.
Last year, I read the best pricing advice I've ever heard. I can't find the link, but the basic concept was to never go for the bargain-minded shopper as your principal sales strategy. There will always be someone new who's willing to sell at a lower price than you--and boom, there go your customers. The bargain hunter is not a loyal customer, and isn't the kind of steady long-term clientele that you want for your business.
I found affirmation of this idea from a surprising source--Warren Buffett. Earlier this month, I read a Wall Street Journal story that interviewed Buffett. This paragraph jumped out at me:
"We do try to buy our businesses like we buy our stocks," Mr. Buffett told me, "and buy our stocks like we buy our businesses." By that he means, among other things, that he wants to understand how the enterprise generates cash, how well-managed it is and whether its customers would stay loyal even if it raised the prices of its goods or services.
There you have it. Unless you're able to make it up on sales volume, you'll never make it in any line of business, handmade or not, if you try to compete on a pricing basis--there are too many other sellers who are willing to take less than you. Go for quality, customer service, honing your own unique style, and figuring out other ways to build customer loyalty--and maybe someday Buffett will invest in you. Hey, you never know.
Monday, November 24, 2008
someday, perhaps I'll remember ...
... that when I use black dye, the dye is at a much higher concentration than the other colors, and will run a lot more. So when I put it in the middle of a skein, it will spread a lot further than the other colors when I wrap it up in plastic to steam it.
Sigh. Someday I'll stop relearning these lessons the hard way.
But maybe this won't be an issue for too much longer. I've been thinking for a while that I'd like to cut down on my use of plastic as much as possible. I recently saw a presentation by the director of the Port Townsend Marine Science Center on the problem of massive plastics pollution in the world's oceans. It was kind of horrifying, actually. The poster child for the problem is the Laysan albatross, where each breeding pair produces one chick a year. The parents fly for many miles in search of food to bring back to their chick, and in recent years, they've been mostly bringing back plastic. A 1994 study autopsied 251 albatross chicks; only six did not have plastic in their digestive system. (Another source says that the most commonly found item is a Bic lighter.) The plastic causes malnutrition of course, since the parents aren't bringing back real food; it also causes blockages that keep the chicks from getting rid of squid beaks and other nondigestibles.
Anyway. I want to cut down on how much plastic I use. I try to be conscious of the packaging of the items that I buy, I reuse ziplocs, etc. I also want to try to do something about how I dye, since my current method of handpainting involves wrapping skeins in plastic wrap before steaming. I was thinking that I might get a steamer pan set, but because each pan has holes, all the skeins would need to be the same colorway and be precisely arranged so that the dye dripping through the holes didn't discolor the skein below. There are those big restaurant chafing dishes, but those are pretty expensive. I could put them in the oven, but I'm trying to get my dyeing work out of the kitchen. Yeah, I'm not sure what the answer is yet.
Sigh. Someday I'll stop relearning these lessons the hard way.
But maybe this won't be an issue for too much longer. I've been thinking for a while that I'd like to cut down on my use of plastic as much as possible. I recently saw a presentation by the director of the Port Townsend Marine Science Center on the problem of massive plastics pollution in the world's oceans. It was kind of horrifying, actually. The poster child for the problem is the Laysan albatross, where each breeding pair produces one chick a year. The parents fly for many miles in search of food to bring back to their chick, and in recent years, they've been mostly bringing back plastic. A 1994 study autopsied 251 albatross chicks; only six did not have plastic in their digestive system. (Another source says that the most commonly found item is a Bic lighter.) The plastic causes malnutrition of course, since the parents aren't bringing back real food; it also causes blockages that keep the chicks from getting rid of squid beaks and other nondigestibles.
Anyway. I want to cut down on how much plastic I use. I try to be conscious of the packaging of the items that I buy, I reuse ziplocs, etc. I also want to try to do something about how I dye, since my current method of handpainting involves wrapping skeins in plastic wrap before steaming. I was thinking that I might get a steamer pan set, but because each pan has holes, all the skeins would need to be the same colorway and be precisely arranged so that the dye dripping through the holes didn't discolor the skein below. There are those big restaurant chafing dishes, but those are pretty expensive. I could put them in the oven, but I'm trying to get my dyeing work out of the kitchen. Yeah, I'm not sure what the answer is yet.
Friday, November 21, 2008
celebrating Thanksgiving a little early this year
I hear stories about bad things happening to good people. To friends and to strangers alike. And aside from making me terribly sad, it also makes me so very grateful for what I have.
I am thankful for a child who is happy, healthy, funny, compassionate, and loving.
I am thankful for a husband who loves me and supports me in all that I do (or try to do), and whom I love.
I am thankful for parents who gave me so many opportunities.
I am thankful for health insurance that has been adequate for all of our medical needs (so far).
I am thankful for wonderful people who have graced my life with their friendship.
I am thankful for a reliable paycheck and flexible schedule that allow me to pursue my love of dyeing.
I am thankful for the lovely customers who support my business, especially the many who have become my friends as well.
I am thankful for my good health.
I am thankful for the opportunity to live in a beautiful part of the world.
What are you thankful for?
I am thankful for a child who is happy, healthy, funny, compassionate, and loving.
I am thankful for a husband who loves me and supports me in all that I do (or try to do), and whom I love.
I am thankful for parents who gave me so many opportunities.
I am thankful for health insurance that has been adequate for all of our medical needs (so far).
I am thankful for wonderful people who have graced my life with their friendship.
I am thankful for a reliable paycheck and flexible schedule that allow me to pursue my love of dyeing.
I am thankful for the lovely customers who support my business, especially the many who have become my friends as well.
I am thankful for my good health.
I am thankful for the opportunity to live in a beautiful part of the world.
What are you thankful for?
Thursday, November 13, 2008
dye studio progress
I got some really thrilling news this week! For next year's Puget Sound yarn shop tour, one of my yarn lines will be the featured yarn for Apple Yarns. It's going to be fantastic business exposure for me, and to say that I'm excited is a huge understatement.
I'm now in the process of looking for a one-skein pattern that will work with my yarn for the store to hand out. I'm talking with a few designers now, plus I also have a fingerless mitt pattern of my own that might possibly work. When I meet with the store owner, I'd like to offer her a few options to choose from. The rest may become kits, which is an idea I've been wanting to explore for a while.
All this makes converting the garage into a dye studio even more important. Last weekend, we put in a utility sink, which was probably the most labor intensive portion of the conversion. To make the pipes as short as possible, we hooked it up right next to the washer. I used it for the first time today, and noticed immediately that I'll need some sort of adjacent work surface to put dye bottles and such. I like the idea of a cabinet on casters that I can use for storing my bottles and jars of powdered dye.
I'm still working on getting a burner of some sort out there. I was all set to get a portable induction cooktop--I like its smooth heating surface, energy efficiency, quick heating, and the lack of open flame. But then I read that it only works on pots that magnets will stick to. I tested my dye pots, and a magnet will only stick to one. So it's either get new pots or look for something else.
I'm now in the process of looking for a one-skein pattern that will work with my yarn for the store to hand out. I'm talking with a few designers now, plus I also have a fingerless mitt pattern of my own that might possibly work. When I meet with the store owner, I'd like to offer her a few options to choose from. The rest may become kits, which is an idea I've been wanting to explore for a while.
All this makes converting the garage into a dye studio even more important. Last weekend, we put in a utility sink, which was probably the most labor intensive portion of the conversion. To make the pipes as short as possible, we hooked it up right next to the washer. I used it for the first time today, and noticed immediately that I'll need some sort of adjacent work surface to put dye bottles and such. I like the idea of a cabinet on casters that I can use for storing my bottles and jars of powdered dye.
I'm still working on getting a burner of some sort out there. I was all set to get a portable induction cooktop--I like its smooth heating surface, energy efficiency, quick heating, and the lack of open flame. But then I read that it only works on pots that magnets will stick to. I tested my dye pots, and a magnet will only stick to one. So it's either get new pots or look for something else.
Sunday, November 2, 2008
lighting for my dye studio
It looks like we're going to do some work to our garage to make it into a better dye studio. That's where I do all my handpainting, and now that daylight hours in Washington are shrinking to about four in a day, the first order of business is better lighting, with or without other improvements.
I went to Home Depot today to look at what they have. The cheapest option would be one of those 4" panel work lights with two long skinny bulbs. They're typically fluorescent, but they also come in daylight versions. I wasn't sure which of the many available bulbs would work best; it might take some experimenting to figure it out.
Another option, which I liked better, was halogen work lights. We already have a dual work light with a stand; those lights have 500 watt bulbs, which I find blinding. I think two lights with lower wattages (150w, maybe), one at each end of my table, might work.
Tonight, I stumbled onto Ott-Lites. Now this looks like the ticket--designed for handwork, intended to show true colors at night. The bulbs appear to be far more energy efficient than halogen bulbs, which is a big plus. I like the Craft Plus floor lamp the best, since it's got the highest wattage and seems to provide the most coverage. The catch? It's $170 plus shipping. Joann's is currently out of stock, but if this baby is eligible for their 50% coupons, I'm going to snap one up when they're available again. I should check the local store, too, just in case.
I went to Home Depot today to look at what they have. The cheapest option would be one of those 4" panel work lights with two long skinny bulbs. They're typically fluorescent, but they also come in daylight versions. I wasn't sure which of the many available bulbs would work best; it might take some experimenting to figure it out.
Another option, which I liked better, was halogen work lights. We already have a dual work light with a stand; those lights have 500 watt bulbs, which I find blinding. I think two lights with lower wattages (150w, maybe), one at each end of my table, might work.
Tonight, I stumbled onto Ott-Lites. Now this looks like the ticket--designed for handwork, intended to show true colors at night. The bulbs appear to be far more energy efficient than halogen bulbs, which is a big plus. I like the Craft Plus floor lamp the best, since it's got the highest wattage and seems to provide the most coverage. The catch? It's $170 plus shipping. Joann's is currently out of stock, but if this baby is eligible for their 50% coupons, I'm going to snap one up when they're available again. I should check the local store, too, just in case.
Friday, October 31, 2008
Apple Yarns
I dropped by Apple Yarns this week to see how my yarn looked. I have to confess to a little thrill at seeing my own yarn occupying its very own cubby in a real, honest-to-goodness store. Especially a store that is my favorite yarn store in town. Okay, it was a big thrill.
It seems to be well-received so far. The store owner and I have big plans for the next installment of Huckleberry Knits yarn--I've managed to get a hold of some locally popular base yarn for my colorways. I see a huge box of deliciously squishy yarn coming to my doorstep in my near future.
In the meantime, I'll need to work on the hardest bit of all--coming up with a name for the new yarn line. I'm transitioning all my yarn lines to have Pacific Northwest names, except for my Flying Cloud yarn, which is just too aptly named to change.
It seems to be well-received so far. The store owner and I have big plans for the next installment of Huckleberry Knits yarn--I've managed to get a hold of some locally popular base yarn for my colorways. I see a huge box of deliciously squishy yarn coming to my doorstep in my near future.
In the meantime, I'll need to work on the hardest bit of all--coming up with a name for the new yarn line. I'm transitioning all my yarn lines to have Pacific Northwest names, except for my Flying Cloud yarn, which is just too aptly named to change.
Tuesday, October 28, 2008
in memory of Colleen
Colleen Kueter (cgkueter on Ravelry), a dyer and knitter that I like and admire, has lost her battle with cancer. She has left behind a 5-year-old daughter and 2-year-old son. The wonderful women at Tiny Lady Cooperative are hosting a benefit for her, beginning today. Per Colleen’s wishes, all proceeds will go to her children’s college fund.
Please help us let Colleen’s family know how much love and support she inspired: http://hyenacart.com/tinyladycooperative
Please bid if anything catches your fancy, buy raffle tickets, make an outright donation, and help to spread the word.
Please help us let Colleen’s family know how much love and support she inspired: http://hyenacart.com/tinyladycooperative
Please bid if anything catches your fancy, buy raffle tickets, make an outright donation, and help to spread the word.
Saturday, October 18, 2008
fiber show wrap-up and my first wholesale order
It's a milestone weekend for Huckleberry Knits--my first fiber show and my first wholesale order delivery.
The fiber show went well. There is very little overhead with this show--no lodging or meals, no booth to set up, and no need to acquire a credit card merchant account, as the guild handles all the transactions. So I'm happy with my net. I also have a better idea of what to bring next year. I think that shoppers at this particular show are more interested in finished items, so I'll try to bring some knits next time. I saw a bunch of people that I knew, none of them knitters, spinners, or weavers, so I should have a way to tap into that audience.
Also, I think I'll put some marketing copy on my labels to help describe the yarns. I think that's a skill that I can bring over from writing online listings to selling in real-world venues.
Here's my first wholesale order: eight pounds of soft squishy yarn.

I like how my first wholesale order turned out. I was a little nervous about the timing because I had to wait for my base yarns to come in and I wanted to finish the order before leaving town. The weather is now cold and rainy, so I thought yarn drying time would be really slow. Then it occurred to me that I could put a drying rack right above the heating vent in my bedroom. Voila! Dry yarn in 24-36 hours.
The fiber show went well. There is very little overhead with this show--no lodging or meals, no booth to set up, and no need to acquire a credit card merchant account, as the guild handles all the transactions. So I'm happy with my net. I also have a better idea of what to bring next year. I think that shoppers at this particular show are more interested in finished items, so I'll try to bring some knits next time. I saw a bunch of people that I knew, none of them knitters, spinners, or weavers, so I should have a way to tap into that audience.
Also, I think I'll put some marketing copy on my labels to help describe the yarns. I think that's a skill that I can bring over from writing online listings to selling in real-world venues.
Here's my first wholesale order: eight pounds of soft squishy yarn.

I like how my first wholesale order turned out. I was a little nervous about the timing because I had to wait for my base yarns to come in and I wanted to finish the order before leaving town. The weather is now cold and rainy, so I thought yarn drying time would be really slow. Then it occurred to me that I could put a drying rack right above the heating vent in my bedroom. Voila! Dry yarn in 24-36 hours.
fiber show #1
This morning I dropped off my boxful of yarns (and one lonely braid of BFL roving) at the Whatcom Weavers fiber show.
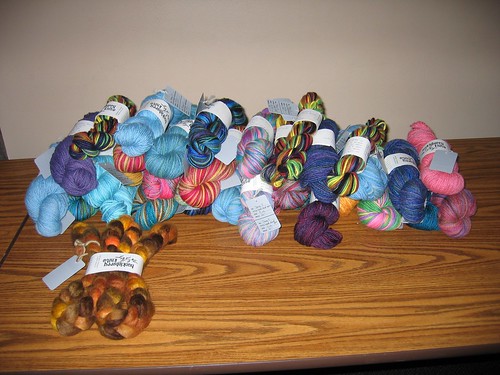
I dropped by after the show opened tonight. The guild members in charge of setup did a fantastic job--nice flow through the tables, attractive grouping of items, lovely decorations. It was especially impressive because they didn't know all of the items they'd be getting until 11 a.m.
The cookie table was conveniently set up near my yarns, so kiddo and I sat and observed the shoppers browsing them. Up until now, my sales have been all online, so I was very curious to see which yarns attracted people, and what they did while deciding whether or not to purchase. In the 10 or 15 minutes we were there, we saw quite a few people rub one particular yarn type and point it out to their friends, though apparently that wasn't quite enough to close the deal right then.
I watched one woman methodically go through one basket of my yarn. She fingered one skein, put it back, went to my next basket. She immediately chose one skein, then went back to the other basket and picked up the one she'd originally looked at and added it to her shopping basket. It's an interesting exercise, trying to figure out what goes through people's minds when they're making purchasing decisions.
Another woman couldn't decide between two of my skeins. They were very different in both weights and color, so that surprised me a bit.
I work the floor tomorrow, so I'm hoping to snap a photo of my display table before it's open to the general public. I tried to get a picture tonight, but there were so many people--much more than either of the last two years, when I went as a customer.
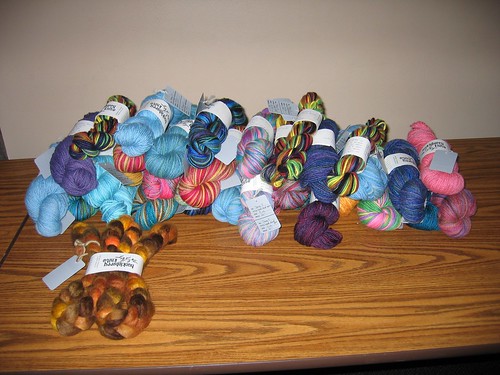
I dropped by after the show opened tonight. The guild members in charge of setup did a fantastic job--nice flow through the tables, attractive grouping of items, lovely decorations. It was especially impressive because they didn't know all of the items they'd be getting until 11 a.m.
The cookie table was conveniently set up near my yarns, so kiddo and I sat and observed the shoppers browsing them. Up until now, my sales have been all online, so I was very curious to see which yarns attracted people, and what they did while deciding whether or not to purchase. In the 10 or 15 minutes we were there, we saw quite a few people rub one particular yarn type and point it out to their friends, though apparently that wasn't quite enough to close the deal right then.
I watched one woman methodically go through one basket of my yarn. She fingered one skein, put it back, went to my next basket. She immediately chose one skein, then went back to the other basket and picked up the one she'd originally looked at and added it to her shopping basket. It's an interesting exercise, trying to figure out what goes through people's minds when they're making purchasing decisions.
Another woman couldn't decide between two of my skeins. They were very different in both weights and color, so that surprised me a bit.
I work the floor tomorrow, so I'm hoping to snap a photo of my display table before it's open to the general public. I tried to get a picture tonight, but there were so many people--much more than either of the last two years, when I went as a customer.
Wednesday, October 15, 2008
I have a yarn problem.
I'm selling yarn at this fiber show this weekend:
http://whatcomweaversguild.org/sale.htm
I originally planned to dye about 50 skeins for the show. After seeing the horrified reactions of the show organizers when I told them, I decided to scale back. Apparently no one else brings nearly that much to sell. My philosophy is more along the lines of "if you don't bring it, you can't sell it," but okay, I didn't want to be the person that all the other guild members whispered about.
So I decided that I was only going to bring the stuff that hadn't sold through my online store (worsted and bulky sell very well because my main market is the soaker/longies crowd, sock and sport do not) or that I had otherwise accumulated, like yarn that needed a bit of touch-up dyeing that I'd never gotten around to doing. No special dyeing for the show. I figured I'd still have about a dozen to bring, while clearing out some space in my cedar chest.
Tonight, while my lovely husband reskeined yarn for my wholesale order, I pulled out everything that I wanted to bring so I could tag it. I still managed to find more than 30 skeins. Where did it all come from? I don't even remember dyeing some of this yarn, which I find to be a little scary--instead of sleepwalking, am I sleepdyeing?
There's quite a bit of sock and sport weight yarn, as I expected. There were a few that didn't photograph well, so I had just put them in the trunk for some future day when I have a better camera or mad photography skillz. But I was surprised to find several skeins of worsted yarn that I'd simply forgotten to sell in my store. It was sort of embarrassing, actually, that they'd gotten buried in the trunk. Too much yarn!
I still need to finish tagging the yarn with both my own tags and ones for the guild. I'll snap a photo tomorrow.
http://whatcomweaversguild.org/sale.htm
I originally planned to dye about 50 skeins for the show. After seeing the horrified reactions of the show organizers when I told them, I decided to scale back. Apparently no one else brings nearly that much to sell. My philosophy is more along the lines of "if you don't bring it, you can't sell it," but okay, I didn't want to be the person that all the other guild members whispered about.
So I decided that I was only going to bring the stuff that hadn't sold through my online store (worsted and bulky sell very well because my main market is the soaker/longies crowd, sock and sport do not) or that I had otherwise accumulated, like yarn that needed a bit of touch-up dyeing that I'd never gotten around to doing. No special dyeing for the show. I figured I'd still have about a dozen to bring, while clearing out some space in my cedar chest.
Tonight, while my lovely husband reskeined yarn for my wholesale order, I pulled out everything that I wanted to bring so I could tag it. I still managed to find more than 30 skeins. Where did it all come from? I don't even remember dyeing some of this yarn, which I find to be a little scary--instead of sleepwalking, am I sleepdyeing?
There's quite a bit of sock and sport weight yarn, as I expected. There were a few that didn't photograph well, so I had just put them in the trunk for some future day when I have a better camera or mad photography skillz. But I was surprised to find several skeins of worsted yarn that I'd simply forgotten to sell in my store. It was sort of embarrassing, actually, that they'd gotten buried in the trunk. Too much yarn!
I still need to finish tagging the yarn with both my own tags and ones for the guild. I'll snap a photo tomorrow.
Sunday, October 12, 2008
my ideal swift
I am in the midst of working on a wholesale order and prepping for a local fiber show this weekend. So my swift and I have been spending a lot of quality time together. (WHEN is my electric skein winder going to get here?)
So I've had ample time to reflect on what features my ideal swift would have:
1) A flexible yet durable method of allowing the swift to adjust to different sizes. With my wooden umbrella swift, the slats are attached to one another with little strings. The slats get tangled together and won’t always open, so I have to shake or pull them apart. And the strings seem to break a lot. It’s on long-term loan from a friend, so I don’t really know how old it is or how much abuse the strings have taken over the years. Maybe these are just OEM strings, in which case I can forgive them.
2) Ball bearings or some other rotational mechanism that would get rid of the wood-on-wood squeaking. I HATE IT. I do a fair amount of winding at midnight or later, and I'm always half-expecting the squeaking to wake up my three-year-old.
3) A deeper and wider table clamp, so I'd be able to attach it to my coffee table and watch a movie while I'm winding. Right now I'm limited to using the swift at my kitchen table. I did discover that I could clamp it to my kitchen counter and watch YouTube videos and other clips on the computer. But my TV screen is a lot bigger than my monitor, and is easier on the eyes.
4) A guide that keeps the loose end of the skein from flapping around. It sometimes/often gets wound up in the rotating part of the swift, causing it to abruptly stop. It’s just an annoyance with heavier yarns, but it breaks sock yarns.
5) Pre-marked circumferences on the central shaft. I.e., put the revolving part at this line, and you’ve got a 2-yard skein; put it at this line and it’s a 2.5-yard skein. If this were my swift, I would just use a marker to indicate the various circumferences. I use masking tape because it's not, but that gets bunched up and eventually wears off.
6) A steadier way to keep the swift at a certain circumference. With this swift, the circumference gradually decreases because the part that rotates around the central shaft doesn’t stay tight. On occasion, it has loosened to the point where the yarn falls off into an untidy heap.
And while we're at it, my fantasy swift would also end world hunger and bring peace and goodwill to all. Hey, it's my fantasy, I get to assign super powers as I like.
So I've had ample time to reflect on what features my ideal swift would have:
1) A flexible yet durable method of allowing the swift to adjust to different sizes. With my wooden umbrella swift, the slats are attached to one another with little strings. The slats get tangled together and won’t always open, so I have to shake or pull them apart. And the strings seem to break a lot. It’s on long-term loan from a friend, so I don’t really know how old it is or how much abuse the strings have taken over the years. Maybe these are just OEM strings, in which case I can forgive them.
2) Ball bearings or some other rotational mechanism that would get rid of the wood-on-wood squeaking. I HATE IT. I do a fair amount of winding at midnight or later, and I'm always half-expecting the squeaking to wake up my three-year-old.
3) A deeper and wider table clamp, so I'd be able to attach it to my coffee table and watch a movie while I'm winding. Right now I'm limited to using the swift at my kitchen table. I did discover that I could clamp it to my kitchen counter and watch YouTube videos and other clips on the computer. But my TV screen is a lot bigger than my monitor, and is easier on the eyes.
4) A guide that keeps the loose end of the skein from flapping around. It sometimes/often gets wound up in the rotating part of the swift, causing it to abruptly stop. It’s just an annoyance with heavier yarns, but it breaks sock yarns.
5) Pre-marked circumferences on the central shaft. I.e., put the revolving part at this line, and you’ve got a 2-yard skein; put it at this line and it’s a 2.5-yard skein. If this were my swift, I would just use a marker to indicate the various circumferences. I use masking tape because it's not, but that gets bunched up and eventually wears off.
6) A steadier way to keep the swift at a certain circumference. With this swift, the circumference gradually decreases because the part that rotates around the central shaft doesn’t stay tight. On occasion, it has loosened to the point where the yarn falls off into an untidy heap.
And while we're at it, my fantasy swift would also end world hunger and bring peace and goodwill to all. Hey, it's my fantasy, I get to assign super powers as I like.
Tuesday, October 7, 2008
Desert Turquoise set
A couple of weeks ago, I finished a set in my Desert Turquoise colorway but forgot to post photos here. I enjoy knitting with my own yarn because I am always curious to see how a colorway turns out. This particular set was for the second knitting customer I ever had, way back in 2005 before I had even considered opening a business. Her enthusiasm for my knitting really helped me to make that leap.
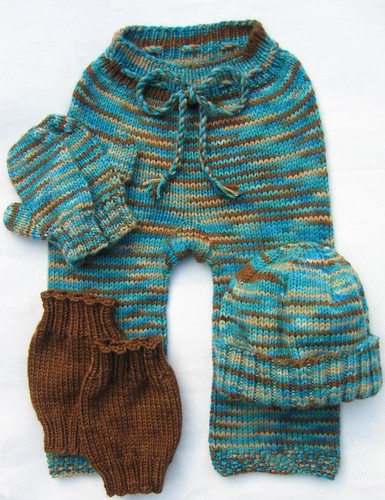
The yarn is aran/light bulky Gaia organic merino, one of my favorites.
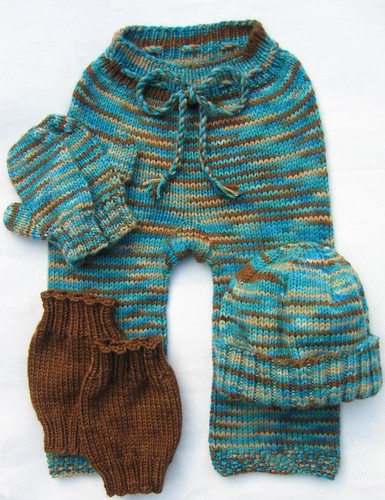
The yarn is aran/light bulky Gaia organic merino, one of my favorites.
Saturday, October 4, 2008
ghost pumpkin hat
I enjoy coming up with new patterns, though most of the time I am too busy with knitting pants to try out anything new. But when Erika asked me to come up with a hat that looked like a ghost pumpkin, to match a pumpkin set that we were working on, I eked out a little bit of time.


This is knitted from natural aran Blue-Faced Leicester. I dyed a little bit of brown yarn for the stem and the vine embellishment. I really like how it turned out, if I may say so.


This is knitted from natural aran Blue-Faced Leicester. I dyed a little bit of brown yarn for the stem and the vine embellishment. I really like how it turned out, if I may say so.
Sunday, September 28, 2008
review: Oregon Flock & Fiber Festival 2008
I did end up going to the Oregon Flock & Fiber Festival this year. I had a few goals in mind: to see I'd want to sell at OFFF (or a similar event) in the future, to do some market research, to check out local fiber processors and the quality of their products, and, oh yeah, to geek out on yarn and fiber.
It was pretty interesting, and I think I got all the info I was looking for. I walked around for a while just to get the lay of the land. The vendors were very roving-oriented, I thought, which matched the customer base--lots of people brought their wheels to spin in classes or on the lawn. I was expecting/hoping to find a lot of local farms who were offering their own finished yarns, stuff that I can't find online or in a normal retail store. And there was some of that, but the majority of vendors were offering commercially produced base yarns and rovings, many of which I already have access to. So not as fruitful as I'd hoped, in that respect.
But it was still very much worth going to. After my first walkthrough, I noted which booths I found most appealing, and then went back for a closer look to figure out why they worked. All of them had easy circulation for casual browsers. I found that narrow entrances that forced me to walk around the person minding the booth were really off-putting. One booth went so far as to put a table to use as the cash wrap about four feet in front of the booth, so as to allow maximum circulation. On such a gorgeous weekend (sunny and 75-80 degrees), that was a great idea.
Some of my favorite booths had beautiful samples front and center, which drew me in to look at their other items. I thought booths with wire cubes for stacking yarns and rovings worked really well, as you could see through them and catch glimpses of other colorways. Opaque dividers have a cleaner background, of course, but I think giving your customers the chance to use their peripheral vision outweighs the less cluttered feel.
It was really cool to walk around and get a feel for what is coming down the pike in the fiber world. For instance, Gotland seems to be an up-and-coming fiber, at least from the producer end. I'm getting a sample of a spun yarn from one of the vendors in a couple of weeks when it's ready; I'm curious to see what it's like.
Probably the most important thing for me as a dyer was seeing the range of normal in hand-dyed yarns. I've been doing a lot more handpainting lately, and I am constantly fretting about depth and consistency of color as compared to other methods. I saw a lot of yarn this weekend, some by big names in the fiber world, and guess what? Their yarn doesn't look like it was turned out by a factory. I know that's obvious, but it really hit home for me this weekend, and it's honestly quite a relief to see that people who have been doing this for years, on a much larger scale than I do, are producing similar results, at least in the aspects that I've been neurotic about. And to a great extent, that's just the nature of the beast. It was so liberating to realize that.
I'm not sure I'll ever be a vendor at OFFF. With the cost of lodging, food, and mileage, I'd need to sell quite a lot to make it worthwhile. At this point in my business, I'm better off selling online and doing a bit of wholesale. But never say never--in a couple of years, as I keep streamlining production, it may end up being a good option for me. Certainly I could see doing this after retiring from my day job; it would be fun to travel around, selling yarn at fiber festivals and competing in dog agility trials.
It was pretty interesting, and I think I got all the info I was looking for. I walked around for a while just to get the lay of the land. The vendors were very roving-oriented, I thought, which matched the customer base--lots of people brought their wheels to spin in classes or on the lawn. I was expecting/hoping to find a lot of local farms who were offering their own finished yarns, stuff that I can't find online or in a normal retail store. And there was some of that, but the majority of vendors were offering commercially produced base yarns and rovings, many of which I already have access to. So not as fruitful as I'd hoped, in that respect.
But it was still very much worth going to. After my first walkthrough, I noted which booths I found most appealing, and then went back for a closer look to figure out why they worked. All of them had easy circulation for casual browsers. I found that narrow entrances that forced me to walk around the person minding the booth were really off-putting. One booth went so far as to put a table to use as the cash wrap about four feet in front of the booth, so as to allow maximum circulation. On such a gorgeous weekend (sunny and 75-80 degrees), that was a great idea.
Some of my favorite booths had beautiful samples front and center, which drew me in to look at their other items. I thought booths with wire cubes for stacking yarns and rovings worked really well, as you could see through them and catch glimpses of other colorways. Opaque dividers have a cleaner background, of course, but I think giving your customers the chance to use their peripheral vision outweighs the less cluttered feel.
It was really cool to walk around and get a feel for what is coming down the pike in the fiber world. For instance, Gotland seems to be an up-and-coming fiber, at least from the producer end. I'm getting a sample of a spun yarn from one of the vendors in a couple of weeks when it's ready; I'm curious to see what it's like.
Probably the most important thing for me as a dyer was seeing the range of normal in hand-dyed yarns. I've been doing a lot more handpainting lately, and I am constantly fretting about depth and consistency of color as compared to other methods. I saw a lot of yarn this weekend, some by big names in the fiber world, and guess what? Their yarn doesn't look like it was turned out by a factory. I know that's obvious, but it really hit home for me this weekend, and it's honestly quite a relief to see that people who have been doing this for years, on a much larger scale than I do, are producing similar results, at least in the aspects that I've been neurotic about. And to a great extent, that's just the nature of the beast. It was so liberating to realize that.
I'm not sure I'll ever be a vendor at OFFF. With the cost of lodging, food, and mileage, I'd need to sell quite a lot to make it worthwhile. At this point in my business, I'm better off selling online and doing a bit of wholesale. But never say never--in a couple of years, as I keep streamlining production, it may end up being a good option for me. Certainly I could see doing this after retiring from my day job; it would be fun to travel around, selling yarn at fiber festivals and competing in dog agility trials.
Wednesday, September 24, 2008
wholesaling
It's official--I am now wholesaling my yarns, and to my favorite local yarn store, to boot! I think it's going to be fun to work with someone local to design a yarn line that's focused on local interests and needs.
I was interested to see that the colorways the store owner was attracted to were nearly identical to the ones that I dyed for my group order in August. There's something about these combinations that seems to appeal to a lot of people.
We're starting off with one of my favorite yarns, Gaia organic sport. I'm also researching a new base yarn to add to my standard ones, which I think will also benefit my online store.
It's really exciting to watch my business grow at a sustainable and comfortable rate. Hurray!
I was interested to see that the colorways the store owner was attracted to were nearly identical to the ones that I dyed for my group order in August. There's something about these combinations that seems to appeal to a lot of people.
We're starting off with one of my favorite yarns, Gaia organic sport. I'm also researching a new base yarn to add to my standard ones, which I think will also benefit my online store.
It's really exciting to watch my business grow at a sustainable and comfortable rate. Hurray!
Saturday, September 20, 2008
some recent knits
I just realized that I haven't posted photos of any knits recently. Here are a few recent customs:
Petals Baby Cardie, knitted from Corriedale in the Flamingos colorway by a time to dye. The sweater is nice, though I didn't care for how the pattern was written. I thought it left some crucial instructions open to interpretation, and then left other things as exercises to the reader.
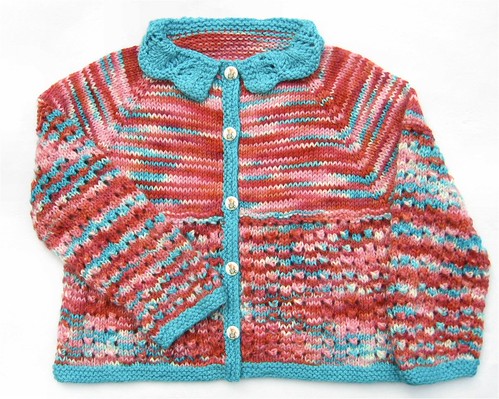
Longies knitted from aran BFL in my Pearl colorway. The customer won 8 oz of custom dyed yarn from me during the Live This Life raffles in the spring. She asked me to hold onto the yarn and knit her some fall longies.
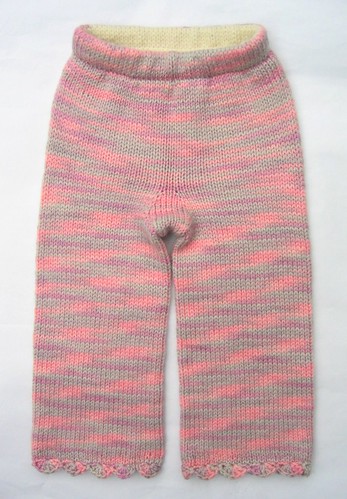
Longies knitted from Cestari fine merino in the Sweet Dragon colorway by Selah. This pair was for a customer who grew up in the town next to the one I grew up in. The internet creates some interesting connections.
Petals Baby Cardie, knitted from Corriedale in the Flamingos colorway by a time to dye. The sweater is nice, though I didn't care for how the pattern was written. I thought it left some crucial instructions open to interpretation, and then left other things as exercises to the reader.
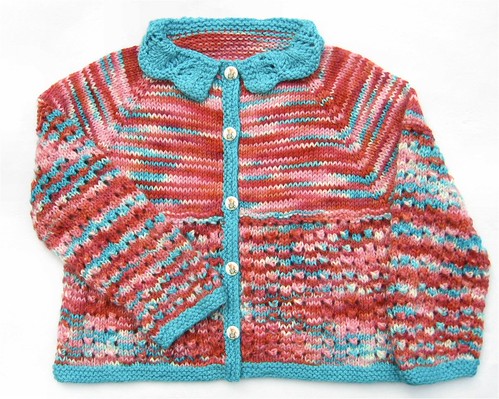
Longies knitted from aran BFL in my Pearl colorway. The customer won 8 oz of custom dyed yarn from me during the Live This Life raffles in the spring. She asked me to hold onto the yarn and knit her some fall longies.
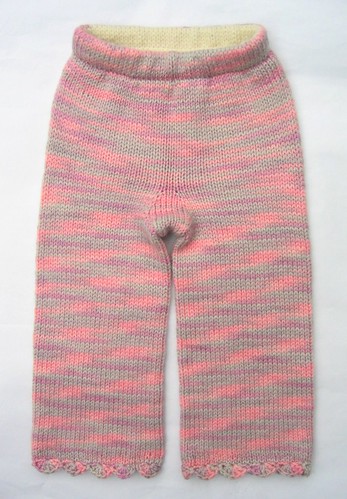
Longies knitted from Cestari fine merino in the Sweet Dragon colorway by Selah. This pair was for a customer who grew up in the town next to the one I grew up in. The internet creates some interesting connections.
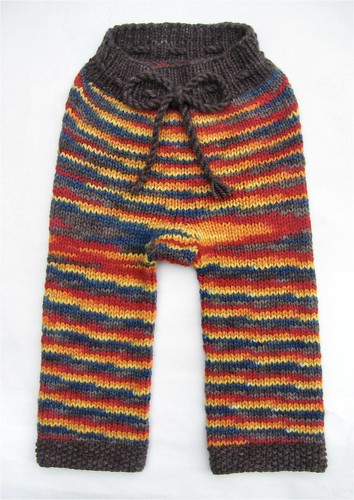
Monday, September 15, 2008
Inked
I'm doing a collaboration with Joline of Hibiscus Baby that goes up tomorrow at Venus Vanguard. Dyed some of my Canadian BFL to match Alexander Henry's Inked Fabric:



I chose to match the primary colors in the fabric, but the other possibility I thought about was matching the subtle, paler shades. I still think that would make a pretty combination. So many ideas, so little time.
No knitting or dyeing tonight, just cooking. I made Tex-Mex pumpkin patties, a pot of curried pumpkin-apple soup, and am in the process of making a batch of granola bars (Nikki & David Goldbeck's American Wholefoods Cuisine).
I also had big plans for food preservation this year, but the only things that've happened were dried strawberries (20 pre-dehydration pounds that disappeared in about a week) and a batch of peach jam. My husband and son ate all the Gravenstein apples that I bought for applesauce, so we'll have to go back to the local orchard again soon. Went huckleberry picking this weekend, but didn't get quite enough for jam.



I chose to match the primary colors in the fabric, but the other possibility I thought about was matching the subtle, paler shades. I still think that would make a pretty combination. So many ideas, so little time.
No knitting or dyeing tonight, just cooking. I made Tex-Mex pumpkin patties, a pot of curried pumpkin-apple soup, and am in the process of making a batch of granola bars (Nikki & David Goldbeck's American Wholefoods Cuisine).
I also had big plans for food preservation this year, but the only things that've happened were dried strawberries (20 pre-dehydration pounds that disappeared in about a week) and a batch of peach jam. My husband and son ate all the Gravenstein apples that I bought for applesauce, so we'll have to go back to the local orchard again soon. Went huckleberry picking this weekend, but didn't get quite enough for jam.
Friday, September 5, 2008
first group order
Before I left on my camping trip the last week of August, I finished up my first group order. Less than three weeks from receiving payment to shipping the yarns--not bad for 30 skeins, considering that I was using this order as a way to work on techniques for increasing my output.

It looks less impressive than when I was winding all those skeins by hand. We had a nasty streak of unusually high humidity and heavy rains for nearly a week, and nothing dried until two nights before I had to get it in the mail. So I spent four hours one night reskeining yarn. The motor for my electric skein winder is still backordered, so neither modern technology nor my husband came to my rescue. Alas.
I'm pretty happy with the results, though. Next up is dyeing for a local fiber show and stocking my store, and then I'll take my next group order in November. There's also a possibility of wholesaling to a local retailer, so I'll be getting together some samples for that as well.

It looks less impressive than when I was winding all those skeins by hand. We had a nasty streak of unusually high humidity and heavy rains for nearly a week, and nothing dried until two nights before I had to get it in the mail. So I spent four hours one night reskeining yarn. The motor for my electric skein winder is still backordered, so neither modern technology nor my husband came to my rescue. Alas.
I'm pretty happy with the results, though. Next up is dyeing for a local fiber show and stocking my store, and then I'll take my next group order in November. There's also a possibility of wholesaling to a local retailer, so I'll be getting together some samples for that as well.
Monday, August 18, 2008
Oregon Flock & Fiber Festival
I'm trying to decide if I want to go to the Oregon Flock & Fiber Festival this year. It's the last weekend of September, about half an hour south of Portland. I can write off the expenses as a business cost, and I think it would be oh so fun to be surrounded by wool, fiber, and the people who love them. I'd really like to source some Pacific Northwest fiber, and this seems like a great opportunity. Not as far as Black Sheep Gathering, which is in Eugene, and close to a cool city that I haven't visited in about 10 years.
My original thought was to take the kiddo with me for the weekend, and give my husband a well-deserved weekend off. But I'm pretty darn sure that a three-year-old's attention span is too limited for me to actually enjoy the event. I'm thinking about floating the idea of the two of them spending Saturday exploring Portland, while I geek out at the fiber festival. Then I hit the parking lot sale on Sunday morning, then we spend the rest of the morning in Portland and drive home in the afternoon.
It has definite possibilities. I'm trying to figure out when to go back to New England to see my parents this fall, and that takes priority, but if the timing works out I'd love to go to my first fiber festival.
My original thought was to take the kiddo with me for the weekend, and give my husband a well-deserved weekend off. But I'm pretty darn sure that a three-year-old's attention span is too limited for me to actually enjoy the event. I'm thinking about floating the idea of the two of them spending Saturday exploring Portland, while I geek out at the fiber festival. Then I hit the parking lot sale on Sunday morning, then we spend the rest of the morning in Portland and drive home in the afternoon.
It has definite possibilities. I'm trying to figure out when to go back to New England to see my parents this fall, and that takes priority, but if the timing works out I'd love to go to my first fiber festival.
Wednesday, August 13, 2008
Cocoa Nouveau
A customer recently asked me to match a popular fabric being used for Goodmama diapers, Cocoa Nouveau. She wanted two browns, two blues, and cream. The browns were easy to match, but the blues were more of a challenge. After a couple of skeins that didn't quite work out, I ended up dyeing some cheap yarn about 12 different shades of blue, trying to zero in on the ones that I wanted.
Finally, I came up with a combination that I liked, and that matches pretty well. The fabric is a little washed out--there's more cream in it than shows up in the photo:

Here's another photo of just the variegated colorway plus matching trim:

I like it. It's an elegant combination of colors, and I like how the cream fades in and out of the other colors. It's going to join my regular lineup of colorways.
Finally, I came up with a combination that I liked, and that matches pretty well. The fabric is a little washed out--there's more cream in it than shows up in the photo:

Here's another photo of just the variegated colorway plus matching trim:

I like it. It's an elegant combination of colors, and I like how the cream fades in and out of the other colors. It's going to join my regular lineup of colorways.
Monday, August 11, 2008
sharing information
Today was a dyeing day for me, and my friend Nicolette came over. Before she had kids, she was really into fibers--dyeing with plant materials, weaving, working at a New England textile museum. But then her girls came along, and she didn't want to use all the toxic mordants around them, and the effort of trying to make a living on the craft show circuit got to her.
So it's been quite some time since she has dyed anything. And she hasn't lived in a place with enough floor space for her loom for several years. But she showed me her dyeing notebooks, and I showed her my monstrous tubs of undyed yarns and talked over the issues that I'm working through as I make the leap from small-batch dyeing to production work. It was pretty cool to talk over this stuff with someone who is a teacher, so her interest is in sharing information and knowledge as widely as possible. With other dyers that I've met in person, there's always some reservation there, and not wanting to tread on toes when talking about dyeing, lest the other person think that you're trying to ferret out trade secrets.
Kind of makes me wish I belonged to a guild. Well, actually, I did just join the local weavers' guild, but I suspect it won't be quite the same thing. It would be fun to share information more freely with others, but I also feel myself holding stuff back. I haven't quite decided where I'm at on all this.
So it's been quite some time since she has dyed anything. And she hasn't lived in a place with enough floor space for her loom for several years. But she showed me her dyeing notebooks, and I showed her my monstrous tubs of undyed yarns and talked over the issues that I'm working through as I make the leap from small-batch dyeing to production work. It was pretty cool to talk over this stuff with someone who is a teacher, so her interest is in sharing information and knowledge as widely as possible. With other dyers that I've met in person, there's always some reservation there, and not wanting to tread on toes when talking about dyeing, lest the other person think that you're trying to ferret out trade secrets.
Kind of makes me wish I belonged to a guild. Well, actually, I did just join the local weavers' guild, but I suspect it won't be quite the same thing. It would be fun to share information more freely with others, but I also feel myself holding stuff back. I haven't quite decided where I'm at on all this.
some thoughts about production dyeing
I'm on my third colorway for the co-op right now, and it has definitely been an educational experience.
My first conclusion: I need one of these electric skein winders from Crazy Monkey Creations. I wound several skeins for dyeing yesterday, and my arm is still sore today. The electric winders should be back in stock next week, and I'm going to save up all the reskeining till I get one.
Second conclusion: Don't try a new dyeing technique when you're short on a particular base yarn, to cut down on that gotta-get-it-right stress. Space dyeing is my favorite technique for consistency of color, but it's pretty slow, so I bought some enormous cooling racks and some giant squeeze bottles at a restaurant supply store, and dyed with those. Yes, it was fast--I dyed six skeins in about 90 minutes, versus the four skeins that I space-dyed tonight over three hours. And you can get much shorter color repeats. But I'm having to do a fair amount of tweaking with dye formulas to get the exact shades that I'm looking for, even with colors that I've been dyeing for two years.
Third conclusion: This is a really great way to see how differently base yarns take dye. For example, Gaia merino wicks dye much faster than any other base yarn I have right now. And when you put dye on superwash, it just sits there, where you put it, which can lead to much higher concentrations of color than you expected.
I think that with most of my remaining colorways, I'm going to go to my slow but consistent and proven methods. I'm trying hard to match my stock photos, and boosting my production while experimenting with new techniques is causing more variation than I'd like. I'll be doing a local fiber show in October, so I'll work on perfecting my production dyeing then.
My first conclusion: I need one of these electric skein winders from Crazy Monkey Creations. I wound several skeins for dyeing yesterday, and my arm is still sore today. The electric winders should be back in stock next week, and I'm going to save up all the reskeining till I get one.
Second conclusion: Don't try a new dyeing technique when you're short on a particular base yarn, to cut down on that gotta-get-it-right stress. Space dyeing is my favorite technique for consistency of color, but it's pretty slow, so I bought some enormous cooling racks and some giant squeeze bottles at a restaurant supply store, and dyed with those. Yes, it was fast--I dyed six skeins in about 90 minutes, versus the four skeins that I space-dyed tonight over three hours. And you can get much shorter color repeats. But I'm having to do a fair amount of tweaking with dye formulas to get the exact shades that I'm looking for, even with colors that I've been dyeing for two years.
Third conclusion: This is a really great way to see how differently base yarns take dye. For example, Gaia merino wicks dye much faster than any other base yarn I have right now. And when you put dye on superwash, it just sits there, where you put it, which can lead to much higher concentrations of color than you expected.
I think that with most of my remaining colorways, I'm going to go to my slow but consistent and proven methods. I'm trying hard to match my stock photos, and boosting my production while experimenting with new techniques is causing more variation than I'd like. I'll be doing a local fiber show in October, so I'll work on perfecting my production dyeing then.
Monday, July 28, 2008
wrist warmers
I decided not to knit a soaker--the group has been running ads on Ravelry and perhaps other places, so I didn't want to limit my potential customer base to cloth diaper users with little girls who wear size mediums. So I knitted some wrist warmers instead:


I like 'em. I started making myself a pair two years ago, when I was working on the pattern, but I've only managed to make one. Is it wrong for me to hope they don't sell?
The link to the auction is here:
http://hyenacart.com/prod_details_auction.php?id=47370&vid=1253


I like 'em. I started making myself a pair two years ago, when I was working on the pattern, but I've only managed to make one. Is it wrong for me to hope they don't sell?
The link to the auction is here:
http://hyenacart.com/prod_details_auction.php?id=47370&vid=1253
Friday, July 25, 2008
Zen String
Angelina of Zen String was my first yarn pusher, organizing the co-ops where I got my first undyed yarn, and dyeing me my first custom colorways. I don't buy from other dyers much anymore, seeing as my stash is already far beyond life expectancy, but once in a while I will cave and buy some of her lovely yarn.
In April, Angelina moved halfway across the country--but something happened and she and her four children have been without a permanent home since then. To help remedy this, the fine women of the Tiny Lady Cooperative are organizing a benefit for her, featuring her yarns.
The benefit starts July 29. I'm hoping to knit a soaker for it this weekend--but even if I don't manage to get it finished in time, please stop by and take a look at some of these wonderful items, and help a friend in need.
In April, Angelina moved halfway across the country--but something happened and she and her four children have been without a permanent home since then. To help remedy this, the fine women of the Tiny Lady Cooperative are organizing a benefit for her, featuring her yarns.
The benefit starts July 29. I'm hoping to knit a soaker for it this weekend--but even if I don't manage to get it finished in time, please stop by and take a look at some of these wonderful items, and help a friend in need.
Wednesday, July 23, 2008
victory is mine!
After writing my post last night, I sorted out the bits dyed by independent dyers and e-mailed a friend who expressed interest last year in those types of scraps. Then I posted on one of my online boards and offered the remainder to anyone who might be interested, for the cost of shipping.
Who knew there would be so many people interested? I just packaged up 18 mini and full-size skeins, weighing in at about 2 lbs. I put some more scraps into a bag for the kiddo's preschool. I stuffed the things that I absolutely could not part with (1.5 toddler socks, a barely-started felted bag project, some scraps for a baby hat for the friend who dyed the yarn) into an old diaper bag. Now I have a tote for all the new undyed yarn. Yay!
Who knew there would be so many people interested? I just packaged up 18 mini and full-size skeins, weighing in at about 2 lbs. I put some more scraps into a bag for the kiddo's preschool. I stuffed the things that I absolutely could not part with (1.5 toddler socks, a barely-started felted bag project, some scraps for a baby hat for the friend who dyed the yarn) into an old diaper bag. Now I have a tote for all the new undyed yarn. Yay!
Tuesday, July 22, 2008
living in the shadow of the Great Yarn Depression
My yarn stash is out of control. A couple of months ago, I managed to sort it into entire skeins, which have completely filled a Lane cedar chest, and scraps, which are in a giant Rubbermaid tote. (This is just the dyed yarn; the undyed yarn has its own tote system.)
The scraps are my main problem now. I did get rid of a bunch of them by giving them to my kiddo's preschool to use for art projects and such. But other partial skeins are too big to just toss--I might use it for a hat someday! Or I might finish that other mitten/sock sometime. That yarn over there would be great for felting, if I ever manage to find time to work on that design that's been rattling around my head for two years. Well, that skein, yeah, I'll probably never use it, but someone else might--I ought to just photograph it and list it for sale. You name the scrap, I've got a good reason for keeping it.
I got another 10 lbs of undyed yarn today and I've got another six showing up shortly. I need this freaking tote to be empty so that I can use it for yarn I'm actually going to do something with. But I just can't let go.
It's not like the Great Yarn Depression is going to hit my household anytime soon. I don't know where this instinctive horror of getting rid of yarn is coming from.
The scraps are my main problem now. I did get rid of a bunch of them by giving them to my kiddo's preschool to use for art projects and such. But other partial skeins are too big to just toss--I might use it for a hat someday! Or I might finish that other mitten/sock sometime. That yarn over there would be great for felting, if I ever manage to find time to work on that design that's been rattling around my head for two years. Well, that skein, yeah, I'll probably never use it, but someone else might--I ought to just photograph it and list it for sale. You name the scrap, I've got a good reason for keeping it.
I got another 10 lbs of undyed yarn today and I've got another six showing up shortly. I need this freaking tote to be empty so that I can use it for yarn I'm actually going to do something with. But I just can't let go.
It's not like the Great Yarn Depression is going to hit my household anytime soon. I don't know where this instinctive horror of getting rid of yarn is coming from.
Monday, July 21, 2008
dyer's woad
My friend Lisa gave me a couple of books for my birthday this year, A Dyer's Garden and A Weaver's Garden. I don't have nearly enough yard space to raise any of these plants (the books estimate needing as many as 24 plants to dye a scant 4 oz of yarn), but I've gotten interested in the idea of using ones that are noxious weeds around here. They're plentiful and I'd be doing the rest of the ecosystem a favor by using them for something practical.
I love indigo, but given that it thrives in places like South Carolina and southeast Asia, I can't make a go of growing it here. Dyer's woad has the same chemical (though in smaller amounts) and grows in Great Britain--a similar climate to here. The catch is that to use woad in a non-commercial form that would avoid the use of lye and such, the leaves must be absolutely fresh, so I have to go foraging for them.
So I looked up dyer's woad and it is classified as a Class A noxious weed in this county--a real nasty. I e-mailed the local noxious weed control coordinator, who is a friend of mine, to see if she could recommend any likely patches.
Alas! Except for one tiny patch in Kittitas County, she says that dyer's woad has been eradicated from Washington state. Quite an achievement--usually Class A weeds are unstoppable--but I am selfishly sad for my big plans ending up in the toilet.
She did say that it is still found in Idaho, where I'll be camping next week. I think I'm going to have to lug along some yarn and a dyepot, just in case. Otherwise, I'll probably be experimenting with purple loosestrife and Scotch broom, which are two nasties that are taking over the countryside.
I love indigo, but given that it thrives in places like South Carolina and southeast Asia, I can't make a go of growing it here. Dyer's woad has the same chemical (though in smaller amounts) and grows in Great Britain--a similar climate to here. The catch is that to use woad in a non-commercial form that would avoid the use of lye and such, the leaves must be absolutely fresh, so I have to go foraging for them.
So I looked up dyer's woad and it is classified as a Class A noxious weed in this county--a real nasty. I e-mailed the local noxious weed control coordinator, who is a friend of mine, to see if she could recommend any likely patches.
Alas! Except for one tiny patch in Kittitas County, she says that dyer's woad has been eradicated from Washington state. Quite an achievement--usually Class A weeds are unstoppable--but I am selfishly sad for my big plans ending up in the toilet.
She did say that it is still found in Idaho, where I'll be camping next week. I think I'm going to have to lug along some yarn and a dyepot, just in case. Otherwise, I'll probably be experimenting with purple loosestrife and Scotch broom, which are two nasties that are taking over the countryside.
Saturday, July 19, 2008
Honeycrisp, take 2
A while ago, I dyed an experimental colorway, Honeycrisp, to match this gorgeous knitting bag by Debbie of Beach Plum Kids:
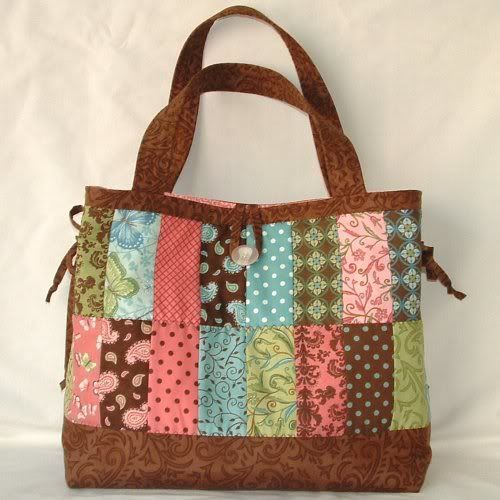
We ended up going with a different colorway, Lark:

So I was free to make the red in Honeycrisp a little darker and richer. I also cut down on the amount of yellow and green. Here's the result, hand-dyed on Flying Cloud:


It turned out just how I wanted it, right down to the dusty green, just like an apple leaf. And the yarn--oh, the yarn. Flying Cloud is so silky smooth, and a light bulky weight so it will work up quickly. It would make a fantastic sweater, except you'd never want to take it off.
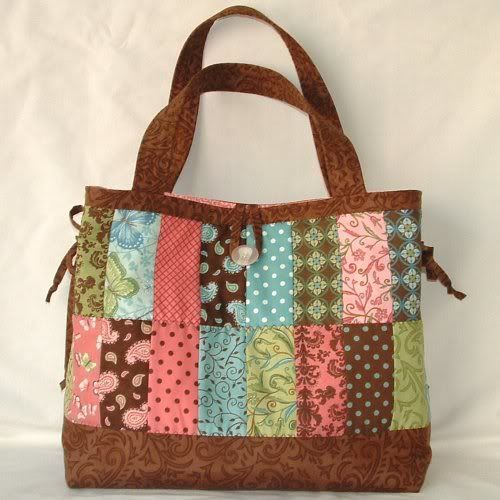
We ended up going with a different colorway, Lark:

So I was free to make the red in Honeycrisp a little darker and richer. I also cut down on the amount of yellow and green. Here's the result, hand-dyed on Flying Cloud:


It turned out just how I wanted it, right down to the dusty green, just like an apple leaf. And the yarn--oh, the yarn. Flying Cloud is so silky smooth, and a light bulky weight so it will work up quickly. It would make a fantastic sweater, except you'd never want to take it off.
Friday, July 18, 2008
waiting for the big brown truck
I am eagerly awaiting a UPS package full of yarn (it's not like I'm already drowning in yarn or anything), but the last time I got a shipping notification from this seller, it was a day before the package actually arrived. So I'm thinking there's probably another peculiar delay between the time they ship and the time the info gets into the system. I wish there were some way to track UPS packages coming to your house by entering your address, and seeing if anything was coming to you.
I took a few photos of my lovely soft Flying Cloud yarn, but they were pretty boring, so I dyed some up instead. I took another shot at Honeycrisp and this time I'm pretty happy with the result. Photos to come this weekend.
I took a few photos of my lovely soft Flying Cloud yarn, but they were pretty boring, so I dyed some up instead. I took another shot at Honeycrisp and this time I'm pretty happy with the result. Photos to come this weekend.
Monday, July 14, 2008
hellooooo, beautiful.
Five kilos of lovely fluffiness just appeared on my doorstep, accompanied by some sock yarn cousins. I've decided to name this particular yarn Flying Cloud. For some reason, I expected this to be plied, but it's bulky soft spun, so the name suits it even better than I thought.
Will update with a photo later--I'm in the middle of dyeing, but I am SO excited to get this yarn!
Will update with a photo later--I'm in the middle of dyeing, but I am SO excited to get this yarn!
Monday, July 7, 2008
she shoots, she scores!
I just nabbed five kilos of bulky BFL/merino, beating two other addicts out by mere minutes. This blend is to die for--the unbeatable softness of merino combines with the strength and luster of Blue-Faced Leicester to form an uncannily silky and gorgeous yarn. It totally was not in my yarn budget but I just could not resist. I'm so excited to get it!
Wednesday, July 2, 2008
Honeycrisp
I have a friend who owns a local apple orchard. Their signature variety is Honeycrisp--one of my favorite eating apples, as sweet and crunchy as their name. When we were in Middlebury, VT a couple of years ago, we bought a 10-lb bag of Honeycrisps at the local farmers' market, intending to bring some home to my parents, whose idea of a good apple is a Red Delicious. Unfortunately, they never got to try one because they were all eaten before we made it back.
This is my first shot at a Honeycrisp colorway. I think I may try adding another shade of deeper red, and reducing the amount of green and yellow.
This is my first shot at a Honeycrisp colorway. I think I may try adding another shade of deeper red, and reducing the amount of green and yellow.

Saturday, June 28, 2008
yarn review: Gaia organic merino
This yarn is a favorite among the soaker/longies knitting crowd, and for good reason. It's wonderfully soft--glides right through your fingers, like silk. An aran weight yarn, so it knits up quickly. My gauge on size 8 needles is about 4.4 stitches to the inch. Takes dye in a somewhat muted way, not as bright as BFL or Clun Forest (the brightest of them all), but the lovely sheen of the yarn adds an interesting depth. One of my personal favorites.
And the sport weight! It could make a sock knitter out of anyone. A lot of yarn comes through my door, but this is the stuff that I want to keep just so I can pet it. Soft as a kitten.
This is my Flying Fish colorway on the aran weight. I dyed it for the Farmers' Market theme at Venus Vanguard, in honor of those kooky fish-throwing guys at Pike Place Market. I think the colors work really well with how the merino accepts dye.
And the sport weight! It could make a sock knitter out of anyone. A lot of yarn comes through my door, but this is the stuff that I want to keep just so I can pet it. Soft as a kitten.
This is my Flying Fish colorway on the aran weight. I dyed it for the Farmers' Market theme at Venus Vanguard, in honor of those kooky fish-throwing guys at Pike Place Market. I think the colors work really well with how the merino accepts dye.
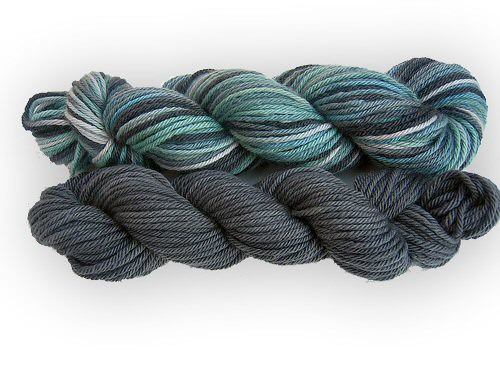
Thursday, June 26, 2008
Flickr for the win
I really admire Carina's photos. She always manages to find a beautiful and often unique angle on her clothing and yarn. I was looking at her new photos in Flickr tonight, and happened to click on her camera type (Nikon D50).
I hadn't realized before that you could search Flickr for all photos taken with a certain camera type, and use search terms. Like, say, yarn. I searched for yarn photos taken with my camera, and the first several pages of photos were, frankly, not that great, even when I searched by "most interesting" (based on views, comments, and number of people marking it as a favorite). I wonder how much of it is who the typical owner of the camera is (i.e., an average sort of photographer who is mostly looking to take snapshots, not fuss with setting up the perfect composition or achieving the perfect lighting), and how much of it is the camera.
Before I get a new camera, I'm going to do a lot of searching in Flickr and Ravelry to find photos of yarn that I really love, and see which camera model(s) were used to take them. Obviously the camera is only one factor in a great photo, but at least I'll get an idea of what the potential is for a given model.
I hadn't realized before that you could search Flickr for all photos taken with a certain camera type, and use search terms. Like, say, yarn. I searched for yarn photos taken with my camera, and the first several pages of photos were, frankly, not that great, even when I searched by "most interesting" (based on views, comments, and number of people marking it as a favorite). I wonder how much of it is who the typical owner of the camera is (i.e., an average sort of photographer who is mostly looking to take snapshots, not fuss with setting up the perfect composition or achieving the perfect lighting), and how much of it is the camera.
Before I get a new camera, I'm going to do a lot of searching in Flickr and Ravelry to find photos of yarn that I really love, and see which camera model(s) were used to take them. Obviously the camera is only one factor in a great photo, but at least I'll get an idea of what the potential is for a given model.
yarn co-ops
I am about to start offering co-ops for my dyed yarns. I have really struggled with what kind of a discount to offer for them. I'm going to try just a small one first and then assess how I feel about the amount of work vs. the reduced profit. There should be some savings in time and increased efficiency; we'll see if they're enough to offset the decrease in money.
I'm also meeting with a local yarn store next week to talk about retailing my yarns locally. I'm really excited about this--it feels like a good step to be taking.
I'm also meeting with a local yarn store next week to talk about retailing my yarns locally. I'm really excited about this--it feels like a good step to be taking.
Monday, June 23, 2008
more adventures in dyeing black
So I finally dyed some yarn with my sorta new black dye, following the instructions. The first two skeins will come out okay, I think, though I'm not entirely sure about the green.
I had some dye left over, so I dyed up a skein of superwash merino that I hadn't used before. This one was a bit of a disaster--the dye did not penetrate evenly, so I had to basically paint individual strands, but I didn't have enough room because of the other two skeins that were still curing in my work space, so the dye job probably wasn't very tidy. And the black dye, which was basically a slurry, got smeared in places where it wasn't supposed to be. Guess this one will be a tester skein for me.
I had some dye left over, so I dyed up a skein of superwash merino that I hadn't used before. This one was a bit of a disaster--the dye did not penetrate evenly, so I had to basically paint individual strands, but I didn't have enough room because of the other two skeins that were still curing in my work space, so the dye job probably wasn't very tidy. And the black dye, which was basically a slurry, got smeared in places where it wasn't supposed to be. Guess this one will be a tester skein for me.
Saturday, June 21, 2008
photo gallery
Ten kilos of fluffy BFL are in da house, and I'm preparing to offer my first yarn co-op. I've decided to reorganize my photo gallery a bit better. With some colorways, I put both detail and full skein pictures in the gallery. Others have just one or the other. So I'm changing all the ones in my gallery to just the thumbnail version, and adding links to the full skein photos and, if I have them, the yarn knitted up. It's a little tedious--okay, a lot tedious--but when I'm done, it will have a tidy uniform look, and I think it will be nice for people to have the links to other photos.
I'm also adding consistent tags. When browsing other, huge galleries, I have dearly wished for a better search function. Mine isn't 10 pages long yet, but better to plan ahead and do it now, rather than go back and do it later for hundreds of photos.
I'm also adding consistent tags. When browsing other, huge galleries, I have dearly wished for a better search function. Mine isn't 10 pages long yet, but better to plan ahead and do it now, rather than go back and do it later for hundreds of photos.
Tuesday, June 3, 2008
my business is growing up
I just placed a $650 wholesale order for yarn today--the largest order I've ever placed. Usually I buy through co-ops, for $100-$200 at a time. But this will be quite the box when it arrives.
I've done a lot of random yarn buys over the past year and a half, seeing what's out there and what I like to work with the best. I've decided now to focus on just my preferred few. The worsted, aran and bulky weights will be sold through my HC store; the sock yarn through a future Etsy store. I've narrowed the heavier yarns down to four types, and the sock yarn to two. It feels good to focus!
It should also help me to better track my inventory. I've got two Rubbermaid tubs of yarn full of undyed yarn. But much to my surprise, when I opened them this weekend to get out some yarn to wind off into skeins, I was down to less than a pound of my two most common types. The shortage was totally camouflaged by all the other yarn. I have to decide now if I want to dye it up and sell it, or probably take a loss and just destash it. I'm leaning towards destashing, because I'm excited about my new direction, but the idea of losing money is never a fun one, of course.
I've done a lot of random yarn buys over the past year and a half, seeing what's out there and what I like to work with the best. I've decided now to focus on just my preferred few. The worsted, aran and bulky weights will be sold through my HC store; the sock yarn through a future Etsy store. I've narrowed the heavier yarns down to four types, and the sock yarn to two. It feels good to focus!
It should also help me to better track my inventory. I've got two Rubbermaid tubs of yarn full of undyed yarn. But much to my surprise, when I opened them this weekend to get out some yarn to wind off into skeins, I was down to less than a pound of my two most common types. The shortage was totally camouflaged by all the other yarn. I have to decide now if I want to dye it up and sell it, or probably take a loss and just destash it. I'm leaning towards destashing, because I'm excited about my new direction, but the idea of losing money is never a fun one, of course.
Sunday, May 25, 2008
cutting it close
Lately, I've had a rash of projects where I've had just enough yarn to do the project. First, there was this pair of shorts, where I had about three yards of yarn left (not blocked in this photo, pardon the lumpiness):

I was pleased that I had enough yarn to get exactly the measurements that I wanted. Didn't have to unravel and fiddle around with the stitch numbers, which is kind of a pain, not to mention anxiety-inducing.
Next came this pair of shorts. I dyed the yarn for these, and estimated that I would need about 5 oz. I had about a foot of yarn left over. I was pretty pleased about that, since I have been wondering what to do with all my leftover bits of skeins. But apparently a foot of yarn does not trigger my pack rat tendencies.

Then six ounces of DK yarn, I think Blue-Faced Leicester, came in the mail. The customer wanted a soaker skirt, but she lives in a hot climate so she didn't want the skirt part to start until the hips, instead of starting up by the waistband. Since it was DK yarn, I decided to do a slightly ruffled skirt with a lace edging, to take advantage of the drapiness and the more delicate stitch size. I ended up with zero leftover yarn on this, except for four inches from the cast-on tail, after I used it to sew up the elastic waistband. Usually when I'm this close on a project, it's on the other side of the line--I'm just a few yards short, and I have to redo big chunks of my project to try to compensate. Can I say how thrilled I am that I didn't have to do that with this skirt?

detail shot of lace edging:

I really love how this turned out. My husband says it's the coolest thing I've ever knitted. "It's pink and it's ruffly, but not too ruffly, and it's feminine but not over the top. Just about perfect, really," he said. High praise indeed.

I was pleased that I had enough yarn to get exactly the measurements that I wanted. Didn't have to unravel and fiddle around with the stitch numbers, which is kind of a pain, not to mention anxiety-inducing.
Next came this pair of shorts. I dyed the yarn for these, and estimated that I would need about 5 oz. I had about a foot of yarn left over. I was pretty pleased about that, since I have been wondering what to do with all my leftover bits of skeins. But apparently a foot of yarn does not trigger my pack rat tendencies.

Then six ounces of DK yarn, I think Blue-Faced Leicester, came in the mail. The customer wanted a soaker skirt, but she lives in a hot climate so she didn't want the skirt part to start until the hips, instead of starting up by the waistband. Since it was DK yarn, I decided to do a slightly ruffled skirt with a lace edging, to take advantage of the drapiness and the more delicate stitch size. I ended up with zero leftover yarn on this, except for four inches from the cast-on tail, after I used it to sew up the elastic waistband. Usually when I'm this close on a project, it's on the other side of the line--I'm just a few yards short, and I have to redo big chunks of my project to try to compensate. Can I say how thrilled I am that I didn't have to do that with this skirt?

detail shot of lace edging:

I really love how this turned out. My husband says it's the coolest thing I've ever knitted. "It's pink and it's ruffly, but not too ruffly, and it's feminine but not over the top. Just about perfect, really," he said. High praise indeed.
Thursday, May 15, 2008
note to self: read the directions
In my quest for a true, reliable black dye, I recently bought some Sabraset. I ASSumed that I could treat it like any other acid dye, but kept getting brownish results. No improvement on using straight Jacquard black.
This week, I was rereading a thread on Ravelry about black dye. I noticed that someone specifically mentioned the importance of following the manufacturer's instructions when using Sabraset. Um, there were instructions? I eventually dug them up on Prochemical's web site. Whoops! Yeah, Sabraset is not like your other, more forgiving dyes, where you can casually toss in some citric acid until it feels right. No wonder the black was striking too soon and turning brown.
So I've learned my lesson--always read the instructions. I'll try overdyeing this weekend, following recommendations, and see if I can rescue my four skeins of organic merino that aren't quite the right shade of black.
This week, I was rereading a thread on Ravelry about black dye. I noticed that someone specifically mentioned the importance of following the manufacturer's instructions when using Sabraset. Um, there were instructions? I eventually dug them up on Prochemical's web site. Whoops! Yeah, Sabraset is not like your other, more forgiving dyes, where you can casually toss in some citric acid until it feels right. No wonder the black was striking too soon and turning brown.
So I've learned my lesson--always read the instructions. I'll try overdyeing this weekend, following recommendations, and see if I can rescue my four skeins of organic merino that aren't quite the right shade of black.
Wednesday, May 7, 2008
business cards
I'm almost out of business cards, so I decided I wanted to redesign them. Spent about an hour working on some variations before I settled on one. Then I spent another two hours trying to upload the file to a certain online print shop. They didn't have my preferred font, and when I converted the font to paths, it looked horrible. And I knew it wasn't just how it looked onscreen--having gotten cards from this place before, I knew that if it looked bad onscreen, it was going to look equally horrid in person.
I tried exporting the file to a bunch of different file formats, and they all looked bad. Plus the colors looked off, so I spent some time tweaking those. Eventually, I uploaded a blank file as the background image (I couldn't just have a blank background), uploaded my logo, and then used one of their house fonts for the rest of the content. Now my eyes hurt and my plans for an evening of knitting are shot. I do graphic design as part of my day job, so I really shouldn't be surprised that these things can eat up so much time ... but somehow I just didn't think it would take so long.
I tried exporting the file to a bunch of different file formats, and they all looked bad. Plus the colors looked off, so I spent some time tweaking those. Eventually, I uploaded a blank file as the background image (I couldn't just have a blank background), uploaded my logo, and then used one of their house fonts for the rest of the content. Now my eyes hurt and my plans for an evening of knitting are shot. I do graphic design as part of my day job, so I really shouldn't be surprised that these things can eat up so much time ... but somehow I just didn't think it would take so long.
Saturday, May 3, 2008
organizing
Spring cleaning fever has hit our household. Today we rearranged some furniture in the house. We have a Lane cedar chest that was full of random junk and never-worn wool sweaters, which we were always bumping into when we tried to go into the master bathroom. Now it's out in the living room and full of yarn. I didn't think that I could get my undyed yarn in there, but I did hope that it would consolidate all of my dyed stash, which is all over the house.
Well, not quite. The stuff that is most easily organized--my yarn from other indie dyers (Beemer Knits, Mosaic Moon, Three Irish Girls, Wooly Wonders by Nada), my Noro, a few skeins of commercially dyed yarn, some colorways that haven't sold yet--are now tidily sorted into little bins inside the chest, and I get a little glow when I look at it. But I still have a Rubbermaid tub and a couple of big tote bags full of odds and ends. I'm a little appalled to find all this fresh evidence of my pack-rattiness.
I've got skein remnants that maybe I could use "someday" for trim or accents or embellishments. Ugly dye jobs that are not fixable. Experimental dyeing partial skeins that are too big to throw away or compost, too small to sell or give away. What on earth am I supposed to do with all this stuff?
I did hear about someone on LJ who solicits yarn donations for her senior center in Massachusetts, so I might contact our local center and see if they'd want it. Or maybe the local preschools could use them for art projects. It seems so wasteful to just junk this yarn, but it's taking up so much darned space--I hope I can find a useful home for at least some of it.
Well, not quite. The stuff that is most easily organized--my yarn from other indie dyers (Beemer Knits, Mosaic Moon, Three Irish Girls, Wooly Wonders by Nada), my Noro, a few skeins of commercially dyed yarn, some colorways that haven't sold yet--are now tidily sorted into little bins inside the chest, and I get a little glow when I look at it. But I still have a Rubbermaid tub and a couple of big tote bags full of odds and ends. I'm a little appalled to find all this fresh evidence of my pack-rattiness.
I've got skein remnants that maybe I could use "someday" for trim or accents or embellishments. Ugly dye jobs that are not fixable. Experimental dyeing partial skeins that are too big to throw away or compost, too small to sell or give away. What on earth am I supposed to do with all this stuff?
I did hear about someone on LJ who solicits yarn donations for her senior center in Massachusetts, so I might contact our local center and see if they'd want it. Or maybe the local preschools could use them for art projects. It seems so wasteful to just junk this yarn, but it's taking up so much darned space--I hope I can find a useful home for at least some of it.
Thursday, May 1, 2008
F5, F5, F5.
I have been hopefully refreshing my Ravelry cart all day, just in case the store opens. I don't know why, but I keep thinking that if only I could buy a Ravelry lapel pin, tote bag, and T-shirt, I could snap out of this funk that I've been in for two days.
Anyway! Enough moping about the lack of retail therapy. I've finally managed to get some good photos of my custom dyeing order. I took some photos yesterday, but I had the not-so-brilliant idea of using a brushed metal tray as the background ... so the yarn got nicely framed by blurry reflections of my face. Whoops. Makes me think of those "accidental" reflections of naked photographers in eBay product photos that were all the rage for a while.
All of these colorways are on bulky Blue-Faced Leicester. I really like this yarn--smooth, silky, and a fast knit.
Copper Patina:

Bloom (really like how this one came out):

Azure:

Decadence:
Anyway! Enough moping about the lack of retail therapy. I've finally managed to get some good photos of my custom dyeing order. I took some photos yesterday, but I had the not-so-brilliant idea of using a brushed metal tray as the background ... so the yarn got nicely framed by blurry reflections of my face. Whoops. Makes me think of those "accidental" reflections of naked photographers in eBay product photos that were all the rage for a while.
All of these colorways are on bulky Blue-Faced Leicester. I really like this yarn--smooth, silky, and a fast knit.
Copper Patina:

Bloom (really like how this one came out):

Azure:

Decadence:

Tuesday, April 29, 2008
my memory is like a wet paper bag
I miss the pre-baby days, when I had a steel trap for a memory, instead of this thing with huge gaping holes. I was dyeing yarn all last week under the assumption that the yarn had been put up in 8 oz skeins. I couldn't figure out why it was sucking up so much more dye than usual, and why it was impossible to twist it into a pretty-looking skein. Till I weighed one, and realized that they were actually one-pound skeins. Why yes, I felt like a total dork--why do you ask?
I feel like I've been slacking off a lot, but somehow in the past week I've managed to dye six pounds of yarn. I've been trying to figure out how much I can realistically wholesale, so it's nice to know that even taking almost half of my nights off, I can still turn out quite a lot of high-quality yarn.
I've been dissatisfied with some of the aran BFL I've gotten lately, so I'm making plans to order from a new supplier next month. I have been experimenting with a bunch of new base yarns lately, but now I'm thinking that I'll focus on my four favorite worsted and aran yarns for my Hyena Cart store, and look towards stocking sock yarn on Etsy. I have my sportweight yarn picked out already, and just need to decide what to use for my fingering weight.
Trying to stock on May 1, but it's only two days away and I have no photos. I need to stop depending on cooperative weather and good outdoor light. Must get off duff and make light box.
I feel like I've been slacking off a lot, but somehow in the past week I've managed to dye six pounds of yarn. I've been trying to figure out how much I can realistically wholesale, so it's nice to know that even taking almost half of my nights off, I can still turn out quite a lot of high-quality yarn.
I've been dissatisfied with some of the aran BFL I've gotten lately, so I'm making plans to order from a new supplier next month. I have been experimenting with a bunch of new base yarns lately, but now I'm thinking that I'll focus on my four favorite worsted and aran yarns for my Hyena Cart store, and look towards stocking sock yarn on Etsy. I have my sportweight yarn picked out already, and just need to decide what to use for my fingering weight.
Trying to stock on May 1, but it's only two days away and I have no photos. I need to stop depending on cooperative weather and good outdoor light. Must get off duff and make light box.
Sunday, April 13, 2008
Picnik love
I have an ongoing struggle with photo editing. Lately, the sorest point has been my thumbnails. When I resize them in either Paint Shop Pro or ArcSoft Photo Studio, they pixelate:

It seems like a new problem, as I can't recall having an issue before. Or maybe I'm just crazy.
Anyway, a few weeks ago, I noticed that Flickr had a new editing option called Picnik. So today I thought, what the heck, I'll try resizing with it. And glory be! whatever protocol it uses to reduce image size works much better. Not perfect, but much less of that weird sparkly static look:

I also signed up for Adobe's new web version of Photoshop, so there's yet another option to play with. But for now, I think Picnik's the way to go for me.

It seems like a new problem, as I can't recall having an issue before. Or maybe I'm just crazy.
Anyway, a few weeks ago, I noticed that Flickr had a new editing option called Picnik. So today I thought, what the heck, I'll try resizing with it. And glory be! whatever protocol it uses to reduce image size works much better. Not perfect, but much less of that weird sparkly static look:

I also signed up for Adobe's new web version of Photoshop, so there's yet another option to play with. But for now, I think Picnik's the way to go for me.
Wednesday, April 9, 2008
no knitting, just photo editing
After three hours, I finally managed to get everything uploaded for my guest stocking at Lily Pad Landing tomorrow. I have no idea why it took me so long to edit photos and come up with names.

I did get distracted by the pooling thread on Ravelry. I really hate ugly pooling, and a lot of the photos people posted would certainly have qualified in my book. Though I was fascinated by how one woman deliberately manipulated pooling to create a chevron effect:

I'll have to keep that concept in mind the next time I run into some uncooperative yarn.

I did get distracted by the pooling thread on Ravelry. I really hate ugly pooling, and a lot of the photos people posted would certainly have qualified in my book. Though I was fascinated by how one woman deliberately manipulated pooling to create a chevron effect:

I'll have to keep that concept in mind the next time I run into some uncooperative yarn.
Friday, March 28, 2008
custom colorway: Funky Giraffe
The lovely Marisa of Funky Giraffe asked me to dye some yarn based on the colors of her store. I've been lacking in boyish inspiration lately, so it was nice to make myself get away from pink and purple for a little while.

There are some subtle changes in blues in this colorway that are hard to see in the reskeined yarn, but I think they'll be more apparent when it's knitted up. Send me a photo please, Marisa!

There are some subtle changes in blues in this colorway that are hard to see in the reskeined yarn, but I think they'll be more apparent when it's knitted up. Send me a photo please, Marisa!
Saturday, March 22, 2008
Flying Fish?
Our next theme for Venus Vanguard is Farmers Market. I was thinking about Pike Place Market, the monster farmers market in Seattle. Its big tourist draw is the guys throwing fish at each other. So I thought maybe a flying fish colorway. Silver, grey, deep teals, with flashes of black and sea green.
I think it has some promise, though I dunno about the name. A few weeks ago, I was reading a book review in People (go ahead, laugh) about a fashionista's pronouncement that nothing named after a fish could possibly be elegant. She was mostly talking about the fishtail dress, which, yeah, ick.
I think it has some promise, though I dunno about the name. A few weeks ago, I was reading a book review in People (go ahead, laugh) about a fashionista's pronouncement that nothing named after a fish could possibly be elegant. She was mostly talking about the fishtail dress, which, yeah, ick.
Wednesday, March 19, 2008
one down, five million to go.
I was pleasantly surprised when I received my 13-lb box of undyed yarn on Saturday instead of Monday. But then I realized that I needed to work on my new colorways on cheap yarn, so I didn't actually dye any of the new yarn till this week.
So far, the week's been a mixed bag. When I was kettle-dyeing my Dusk colorway, I didn't get the dye intensity quite right. Plus I sloshed the yarn around when I took it off the stove, and now it's not Dusk anymore. Very pretty, but not what I was wanting.
I did manage to knock one item off my list--I've dyed up the Eat Your Veggies yarn for my collaboration with Erika. She's going to do an appliqued T-shirt to go with the yarn as part of our Farmers' Market stocking.
As far as knitting goes, I'm taking a break from custom orders because I know I'm going to be crazy busy with the two early-April stockings, and I don't want the stress of a custom right now. So I've picked up my personal Jaywalker sock project again, because my hands feel funny in the evenings if they're not holding knitting needles. I've shortened the gusset by almost an inch from the pattern, because it seemed like it was past time to turn the heel, but the last time I deviated from the pattern I was sorry. I hope I'm not sorry again.
I am torn between dyeing some more yarn tomorrow afternoon, and going with my husband to a sports bar to watch the opening day of March Madness. I'm not sure which option would make me geekier.
So far, the week's been a mixed bag. When I was kettle-dyeing my Dusk colorway, I didn't get the dye intensity quite right. Plus I sloshed the yarn around when I took it off the stove, and now it's not Dusk anymore. Very pretty, but not what I was wanting.
I did manage to knock one item off my list--I've dyed up the Eat Your Veggies yarn for my collaboration with Erika. She's going to do an appliqued T-shirt to go with the yarn as part of our Farmers' Market stocking.
As far as knitting goes, I'm taking a break from custom orders because I know I'm going to be crazy busy with the two early-April stockings, and I don't want the stress of a custom right now. So I've picked up my personal Jaywalker sock project again, because my hands feel funny in the evenings if they're not holding knitting needles. I've shortened the gusset by almost an inch from the pattern, because it seemed like it was past time to turn the heel, but the last time I deviated from the pattern I was sorry. I hope I'm not sorry again.
I am torn between dyeing some more yarn tomorrow afternoon, and going with my husband to a sports bar to watch the opening day of March Madness. I'm not sure which option would make me geekier.
Thursday, March 13, 2008
Lament.
I am waiting on 20 pounds of undyed yarn right now. Half of it is coming from a wholesaler who was supposed to have shipped last Friday, but somehow misunderstood my e-mail that said I didn't want to wait for the backordered yarn that just arrived today. The other half is from a co-op, and part of my order won't arrive till next week so it will be another week before I get it.
Normally it's no big deal. My usual problem is trying to get through all the yarn that I've got in the house. But right now, thanks to my increased financial discipline for business-related spending this year, all I've got is bulky BFL and I'm needing some aran/worsted weight yarn to dye up for early April knitting projects. Bah, I knew this budgeting thing was a bad idea.
A little list of what I've got in mind for projects:
For my guest stocking at Lily Pad Landing, I'm planning to dye my Daydream and Spring Skies colorways. Got Daydream dyed up today on my last skein of Gaia organic merino, but I'm a little uncertain about how it turned out and will have to see what it looks like dry. I also want to do a skirt with my flowering plum embellishment:
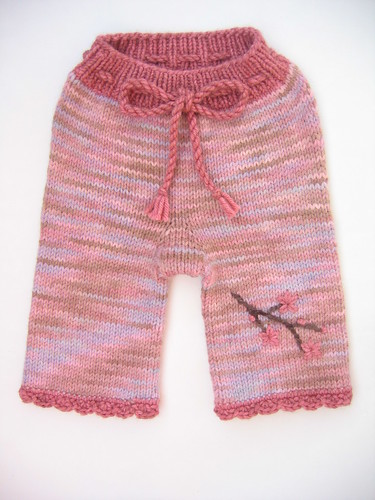
but I haven't figured out what I want my base colorway to be. I'd also like to do a boyish knitted item, or maybe a felted purse ... not sure yet.
Then my own congo, Venus Vanguard is doing a Farmers' Market theme around the same time. I need to dye up Eat Your Veggies for a collaboration with Erika of Ramie Baby Designs. I have a Honeycrisp apple colorway in mind, for which I should probably do some experimental dyeing on cheap yarn this weekend. And I want to come up with another colorway, too. Maybe a sweet pea one?
After several months, I'm still thinking about approaching a local yarn store about carrying my yarns. Because they tend to take a significant percentage, I would probably need to raise my prices across the board, which I'm reluctant to do. I feel like I'm at a pretty good price point for my main target audience. But the thought of not spending hours taking photographs and struggling with color correction is awfully appealing.
Normally it's no big deal. My usual problem is trying to get through all the yarn that I've got in the house. But right now, thanks to my increased financial discipline for business-related spending this year, all I've got is bulky BFL and I'm needing some aran/worsted weight yarn to dye up for early April knitting projects. Bah, I knew this budgeting thing was a bad idea.
A little list of what I've got in mind for projects:
For my guest stocking at Lily Pad Landing, I'm planning to dye my Daydream and Spring Skies colorways. Got Daydream dyed up today on my last skein of Gaia organic merino, but I'm a little uncertain about how it turned out and will have to see what it looks like dry. I also want to do a skirt with my flowering plum embellishment:
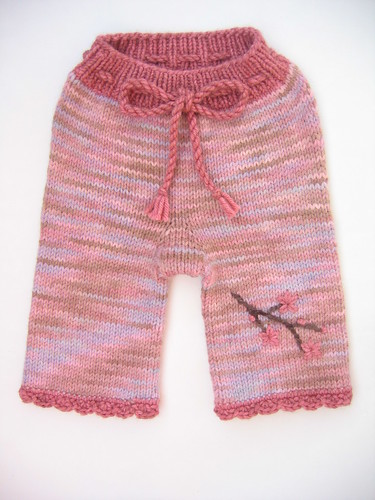
but I haven't figured out what I want my base colorway to be. I'd also like to do a boyish knitted item, or maybe a felted purse ... not sure yet.
Then my own congo, Venus Vanguard is doing a Farmers' Market theme around the same time. I need to dye up Eat Your Veggies for a collaboration with Erika of Ramie Baby Designs. I have a Honeycrisp apple colorway in mind, for which I should probably do some experimental dyeing on cheap yarn this weekend. And I want to come up with another colorway, too. Maybe a sweet pea one?
After several months, I'm still thinking about approaching a local yarn store about carrying my yarns. Because they tend to take a significant percentage, I would probably need to raise my prices across the board, which I'm reluctant to do. I feel like I'm at a pretty good price point for my main target audience. But the thought of not spending hours taking photographs and struggling with color correction is awfully appealing.
Wednesday, March 12, 2008
the Huckleberry colorway
For over a year now, I've been thinking about a huckleberry colorway. I thought it would have purple and green for sure, and possibly some silvery grey like the twigs of a huckleberry bush. But I never got around to dyeing it because there was something missing from the image in my head.
A couple of weeks ago, I was developing a colorway for my spring training swap partner on Ravelry. It was supposed to be deep reds and blues, with some purples where the colors overlapped. But through the magic of kettle dyeing, the experimental skein turned into something quite different and wholly charming. When the skein had dried, I took it into natural daylight and the rich purples and wine reds leaped out at me. It looked just like a bowlful of freshly washed huckleberries. And I knew I'd gotten my namesake colorway.

A couple of weeks ago, I was developing a colorway for my spring training swap partner on Ravelry. It was supposed to be deep reds and blues, with some purples where the colors overlapped. But through the magic of kettle dyeing, the experimental skein turned into something quite different and wholly charming. When the skein had dried, I took it into natural daylight and the rich purples and wine reds leaped out at me. It looked just like a bowlful of freshly washed huckleberries. And I knew I'd gotten my namesake colorway.


Friday, February 29, 2008
cousins under the skin--er, overdye
Seems like lately I've been dyeing a lot of warm yellows, so rather than mixing it everytime, I got some golden yellow dye. I was messing around with it one night, trying to get a colorway that was something like this, only with a little turquoise:

Instead, I got this:
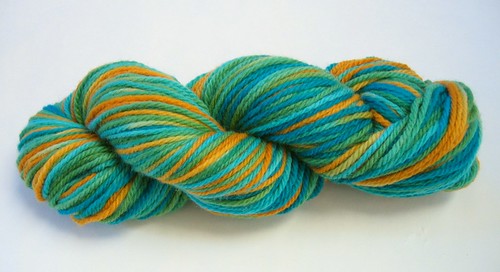
And a subsequent try was a little sloppy--I didn't make the color repeats long enough, and everything bled as the dye was setting, so I resorted to my old friend the navy overdye:

Strange to think that these two colorways are actually related. Sort of like the way human beings share 90+ percent of their genes with apes, yet turned out rather differently. That's what's so interesting and frustrating about dyeing: how what you plan is so often not what happens.

Instead, I got this:
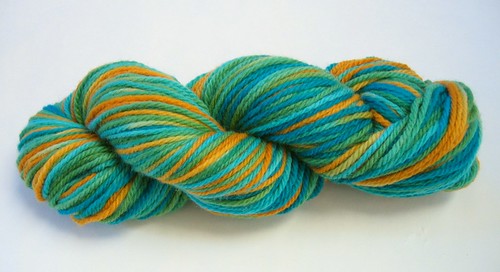
And a subsequent try was a little sloppy--I didn't make the color repeats long enough, and everything bled as the dye was setting, so I resorted to my old friend the navy overdye:

Strange to think that these two colorways are actually related. Sort of like the way human beings share 90+ percent of their genes with apes, yet turned out rather differently. That's what's so interesting and frustrating about dyeing: how what you plan is so often not what happens.
Subscribe to:
Posts (Atom)